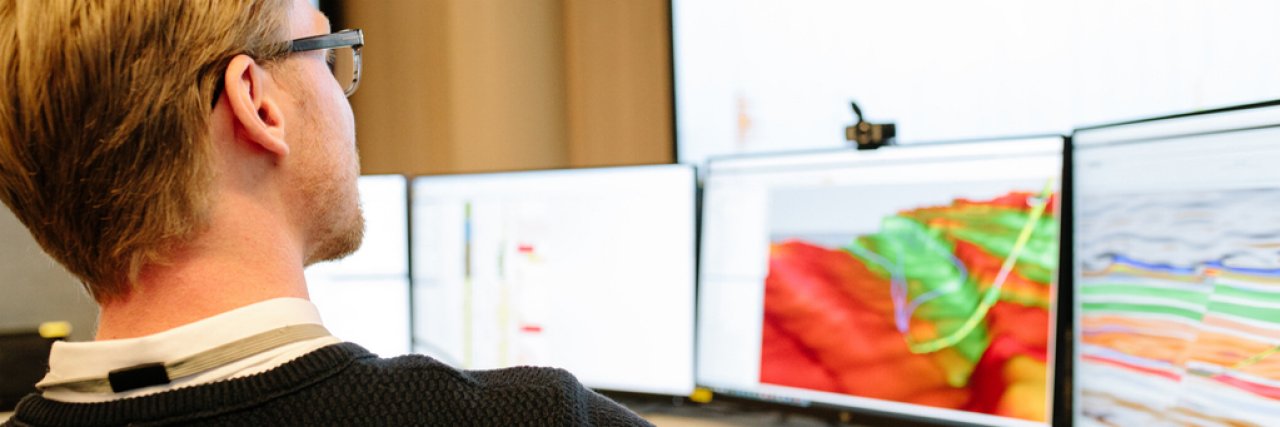
Let’s get REAL
REAL helps our geoscientists see what kind of rock they’re drilling through in real time. Here’s how the magic happens.
You might think that drilling a well is a straight-forward task - but that’s as far away from the truth as you can get. Our geoscientists need to know what we’re drilling through and encountering to make sure our wells are as productive as they can be.
The geoscientists have an eye on the drilling operation at all hours of the day, observing and looking at a variety of data and logs to be able to interpret the lithology, basically what type of rock, we’re encountering.
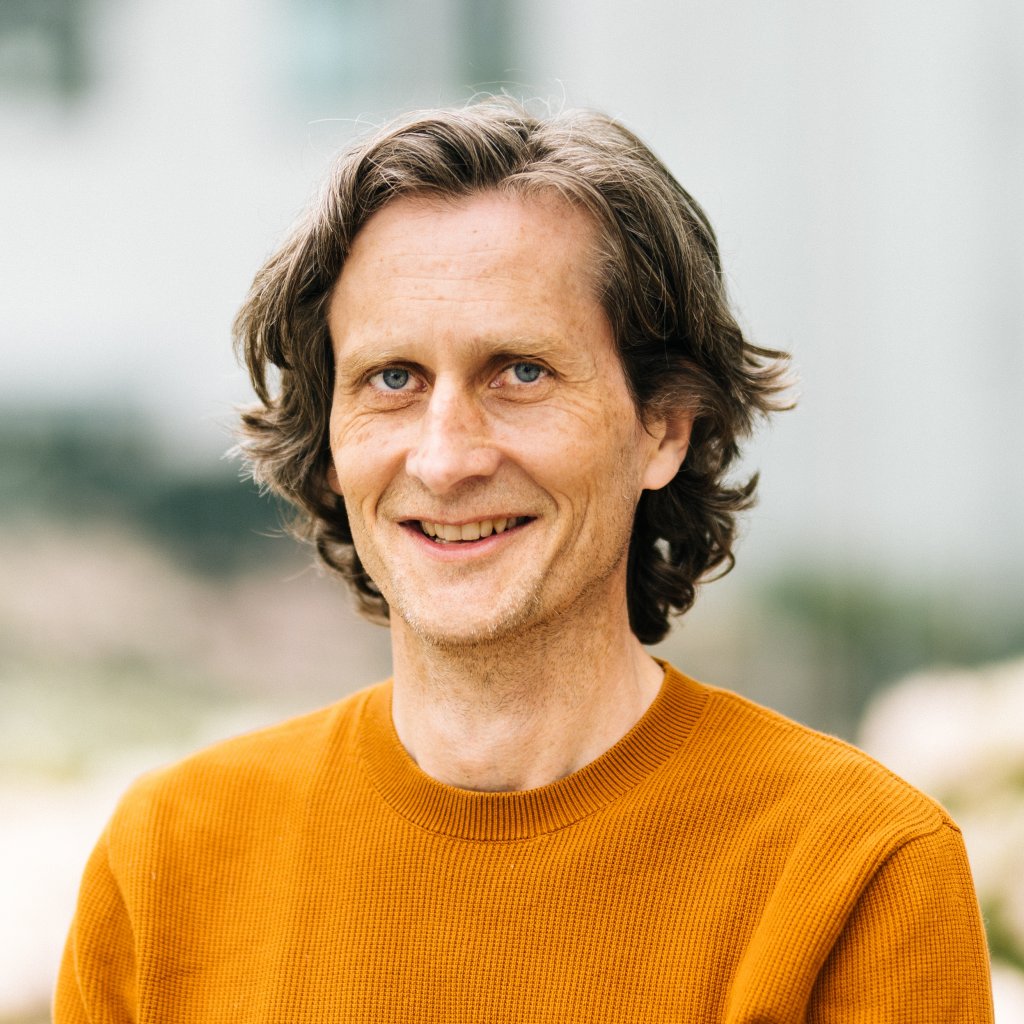
“REAL can automatically interpret the kind of rock we’re drilling in and what kind of geological risks we might encounter - all in real time. It’s an impressive combination of machine learning, petrophysical algorithms and expert knowledge.”
Harald Eggen, software developer
Harald works as a developer on the REAL team and has helped bring machine learning both into the depths of the subsurface - and to the Geo Operations Center (GOC).
There, geologists and geoscientists keep a 24/7 eye on all our drilling operations for Norwegian development wells. They give input and make decisions on well placement, as well as helping the drilling rig to drill the well in the safest way.
REAL at a glance
- Machine-learning using drilling parameters and LWD logs to interpret lithology and geological risks at the bit
- REAL is short for “Real time automated lithology” and is an Equinor inhouse developed software
- Contributes to safer drilling, tripping and running of casing/liner, more effective and cheaper wells
- Uses a combination of machine learning and analytical petrophysical models
- Written in python and uses boosted trees machine learning algorithms
- Running in Azure with connectivity to Equinor internal network and real time databases
Drilling a well is a step-by-step process that can resemble the Russian babushka dolls that have another doll inside them. First, we use a drill bit to drill a hole in the rock. Then, we take it back out and install piping to keep the well from collapsing.
All of this is repeated in stages and completing a well can take anything from weeks to months. The data they get in real time from REAL is data they previously had to enter manually, and it wouldn’t be available for the drilling crew until hours later.
“REAL doesn’t just make work easier: it also helps in getting us consistent lithology interpretations and is available to both drilling rig and onshore offices at all times.”
Linn Arnesen, geologist
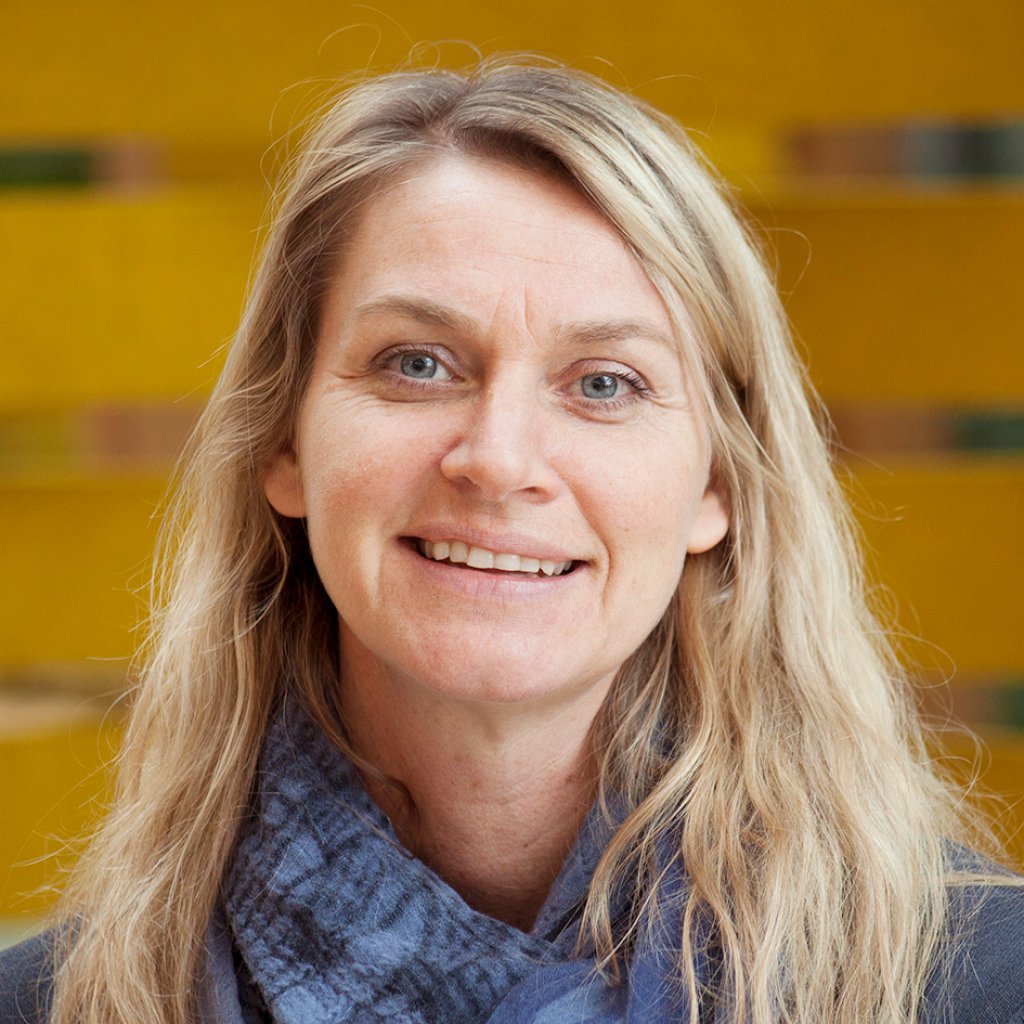
Linn is one of the geologists working at the GOC, after having spent the last couple of years as the REAL project leader. There, she’s now able to enjoy the perks of having the software she helped develop as part of her toolbox.
Ready to find out how it all works and runs? Then let’s crack on into the code!
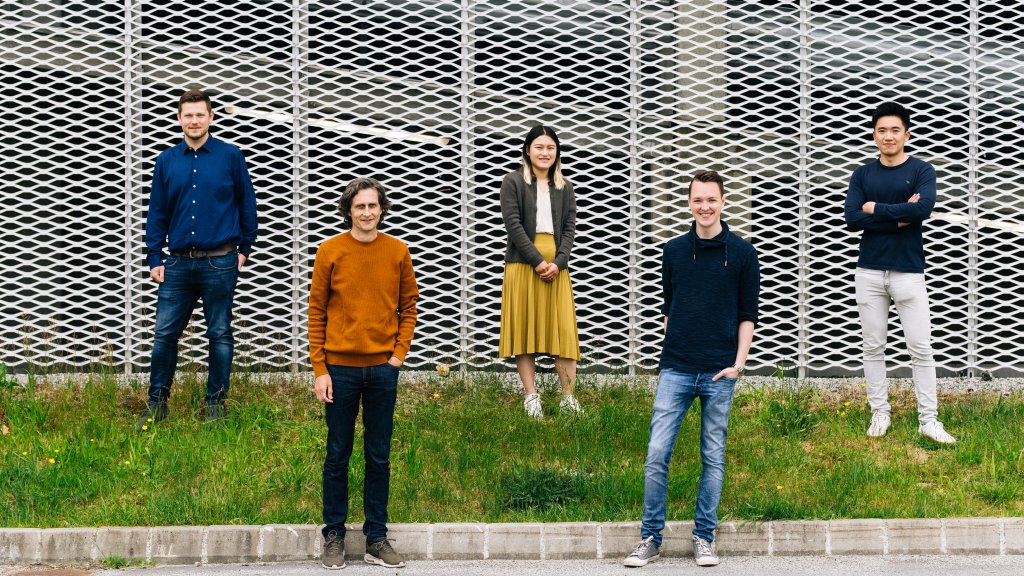
Drill bit sensors and where to find them
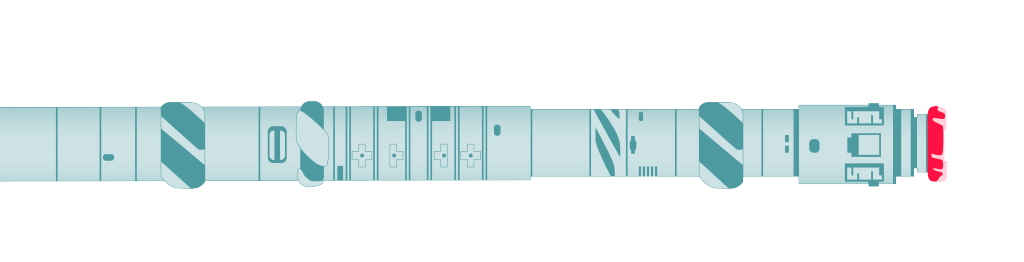
When drilling a well, the drill bit (in red) and bottom hole assembly (BHA) doesn't just do the drilling. It also collects a whole lot of data, which REAL uses.
Sensors are located behind the drill bit, marked in red on the illustration. The most important sensors are gamma ray, resistivity, neutron, density, caliper and gas data.
It's no small bottom hole assembly however - the section you see on the left can be as long as 37 meters!
Balancing the data
These logs that the geologists are looking at come in the form of curves measured along the wellbore. It’s these curves that REAL looks at, processes and feeds back into the software as an interpretation of the type of rock drilled.
Every 15 minutes data is fetched, smoothed, resampled, feature engineered, interpreted and processed - all automated of course.
Today, REAL is used at 5 of our fields and they’re continuously working on adding more, but it all started with Troll. The team trained the network through using data from 180 of the existing wells, which gave them tons of data to work with.
The Geo Operations Centre
Equinor’s Geo Operation Centre (GOC) monitors and manages drilling of the wells offshore. It’s staffed 24/7 by geoscientists and its mission is to ensure more efficient drilling, reduce costs and to provide increased safety.
Almost all production fields of the Norwegian Continental Shelf (NCS) are monitored from the GOC.
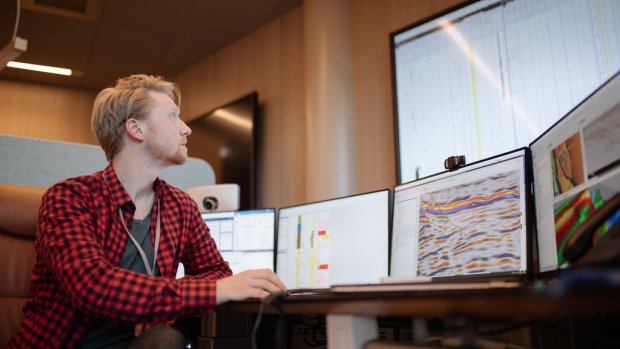
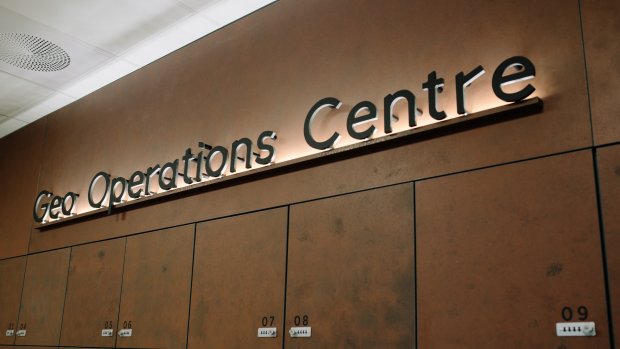
However, they were soon faced with a major challenge. Reservoirs mostly consist of sandstone, but it’s the other types of lithology that might represent a risk during drilling.
“Our training data was highly unbalanced, we had very few datapoints for some of the lithology that’s important to interpret correctly. The solution was to assign a higher weight to those minority datapoints and use a cost function so that the model will penalize more if we incorrectly classify those lithologies,” Harald says.
Since he spent his school years studying signal processing and always had an interest in geology, you might say that Harald hit the jackpot working on REAL.
“It takes a whole lot of domain knowledge, signal processing, machine learning and technology to make REAL work. It really makes me feel part of something bigger than “just IT”.”
Harald Eggen
Stay in the Loop
Focusing on feature engineering
Data is gathered in real time by sensors found a few meters behind the drill bit. Since most wells don’t have a cable from the rig and down to these sensors, the real time data will be transmitted to the surface using mud pulse technology.
The signals are converted to mud pulses that travel a few thousand meters in the mud inside the drill string - before being converted back to electrical signals on the surface. This introduces a lot of noise.
“Dealing with all this noise and processing the data into something you can actually do machine learning with is also a major challenge."
Harald Eggen
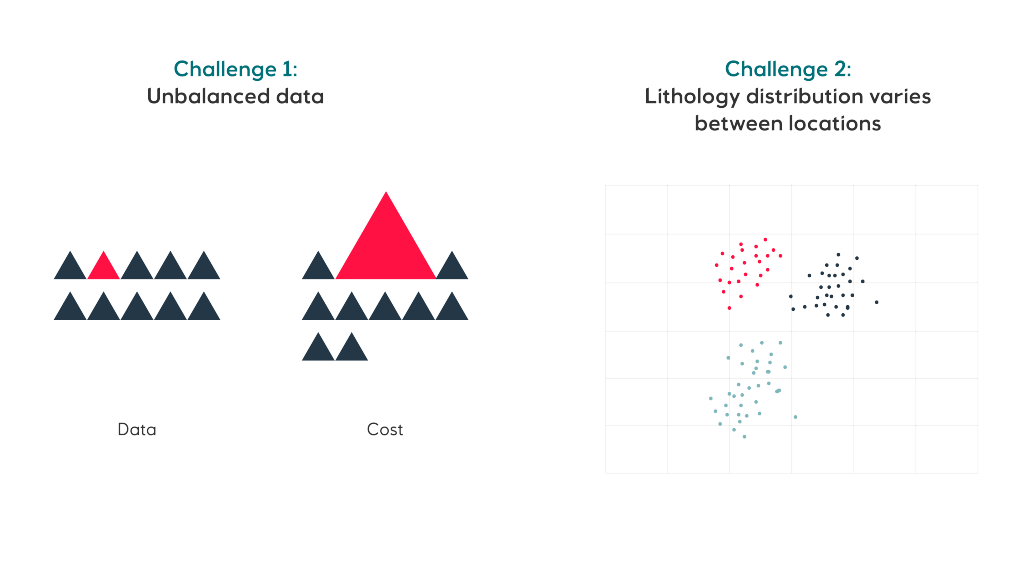
“Since we get real time data it can be a challenge to filter out crazy “spikes” or anomalies in the data. And if there’s missing data, we need to interpret it and make it qualified for the model,” Li Deng says.
Li has spent the last two years working as a developer on REAL. She tells us that while the actual machine learning algorithm is the same for each field, there’s a variety of data available for each field. This means the model needs training for each new field that’s added.
“It’s quite interesting because we have to be creative and smarter with what we have for each field,” Li says.
And it’s clear both their creativity and machine learning model are working.
“We're greedy when it comes to extracting information from the raw data. One cool thing REAL does is that it leverages different domain knowledge in feature engineering. These new features help a lot with improving the accuracy of our ML models.”
Li Deng, software developer
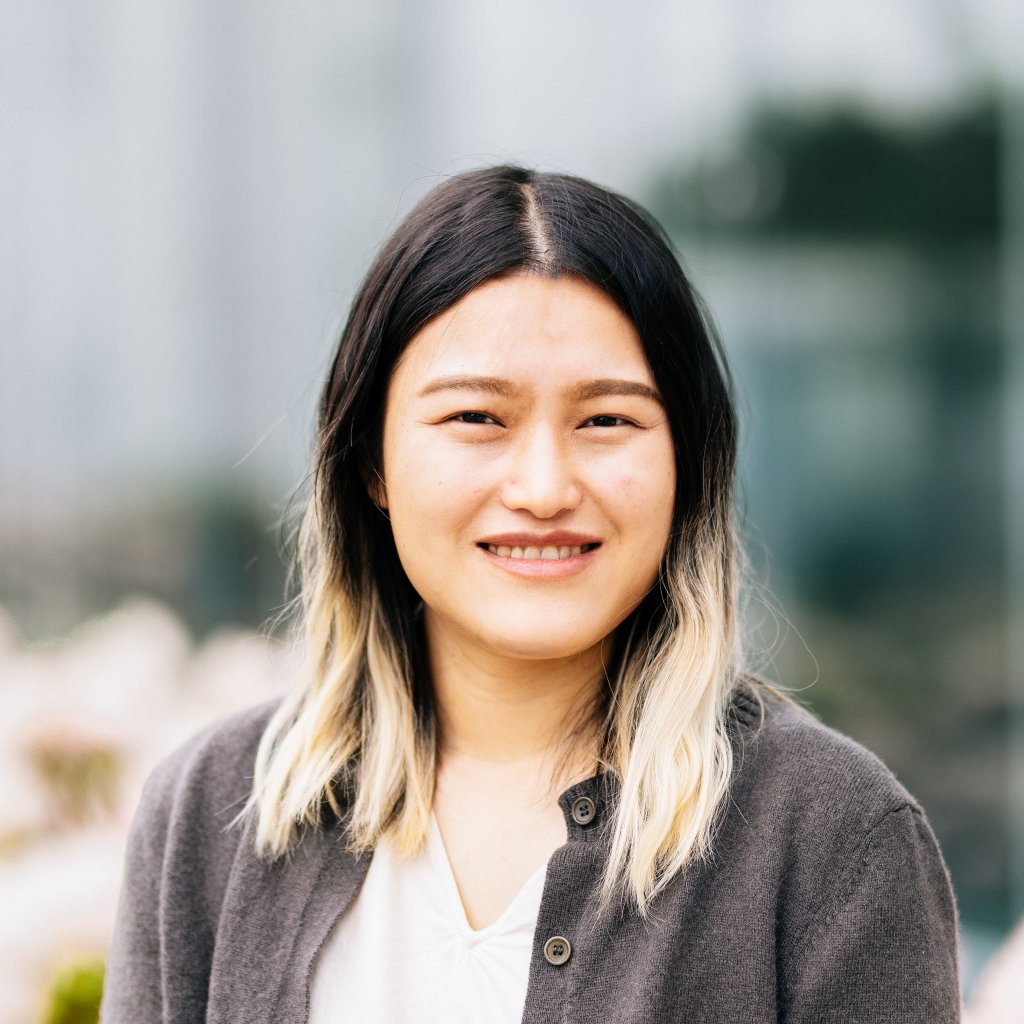
Tiers of REAL
Lithology interpretations happen in steps, named tiers, as the drill bit makes its way into the rock.
Tier 1 is purely based on drilling parameters and is interpreted at actual bit depth at any time
Tier 2 is based on drilling parameters plus gamma ray - and is interpreted at the depth of the gamma ray sensor, usually 3-9 meters behind the bit
Tier 3 - 7 include resistivity, neutron, density, caliper and gas data; later interpreted at the sensor depth of each data type
Tier 8 also includes the petrophysical model for the actual field.
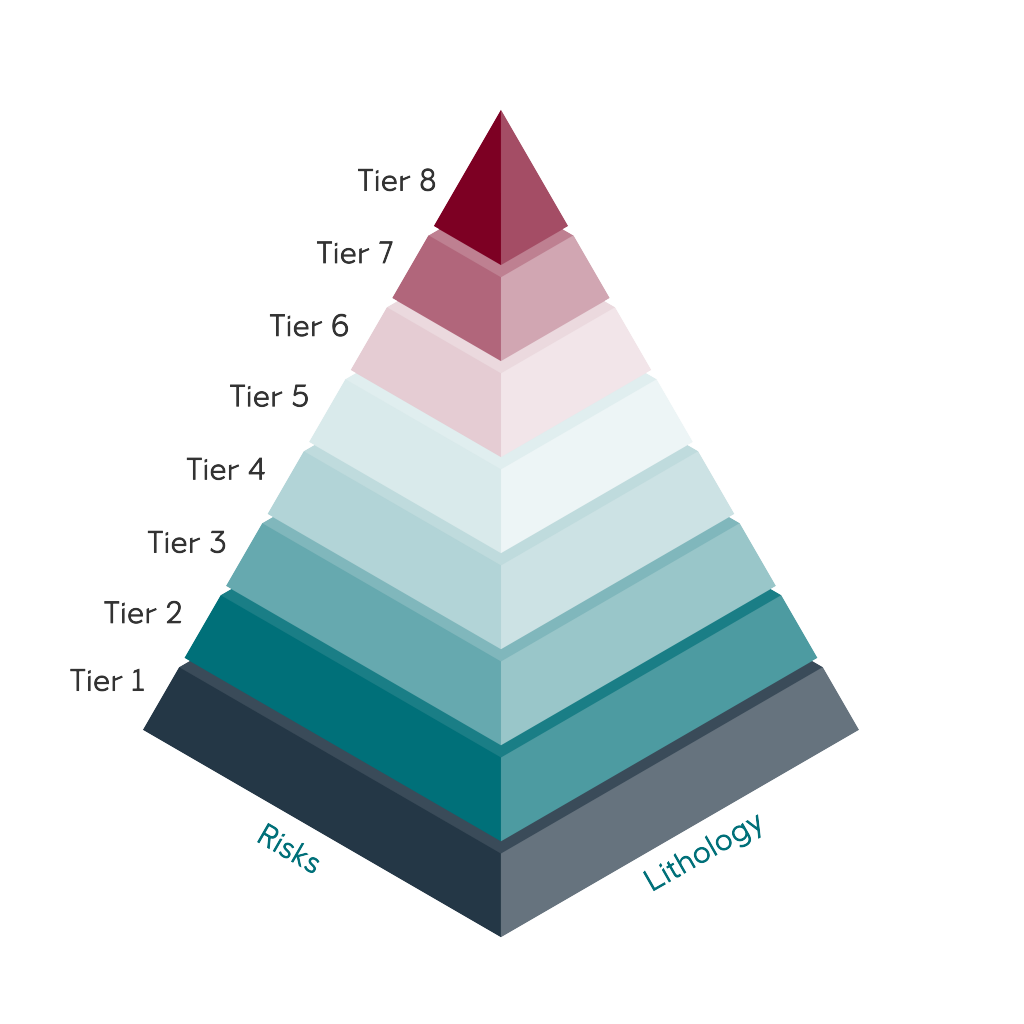
Same procedure as the last field
The main principles stay the same but working with different fields come with their own set of challenges. That’s why the team has to “repeat” the procedure. Let’s walk on through the process for a fictional “Loop” field.
Work starts with accessing historical logs from the Loop field through software used at the GOC in order to begin experimenting with features unique for the field.
“Then, we start training the model through several iterations, which can take anywhere from 2-4 weeks to complete,” Harald explains.
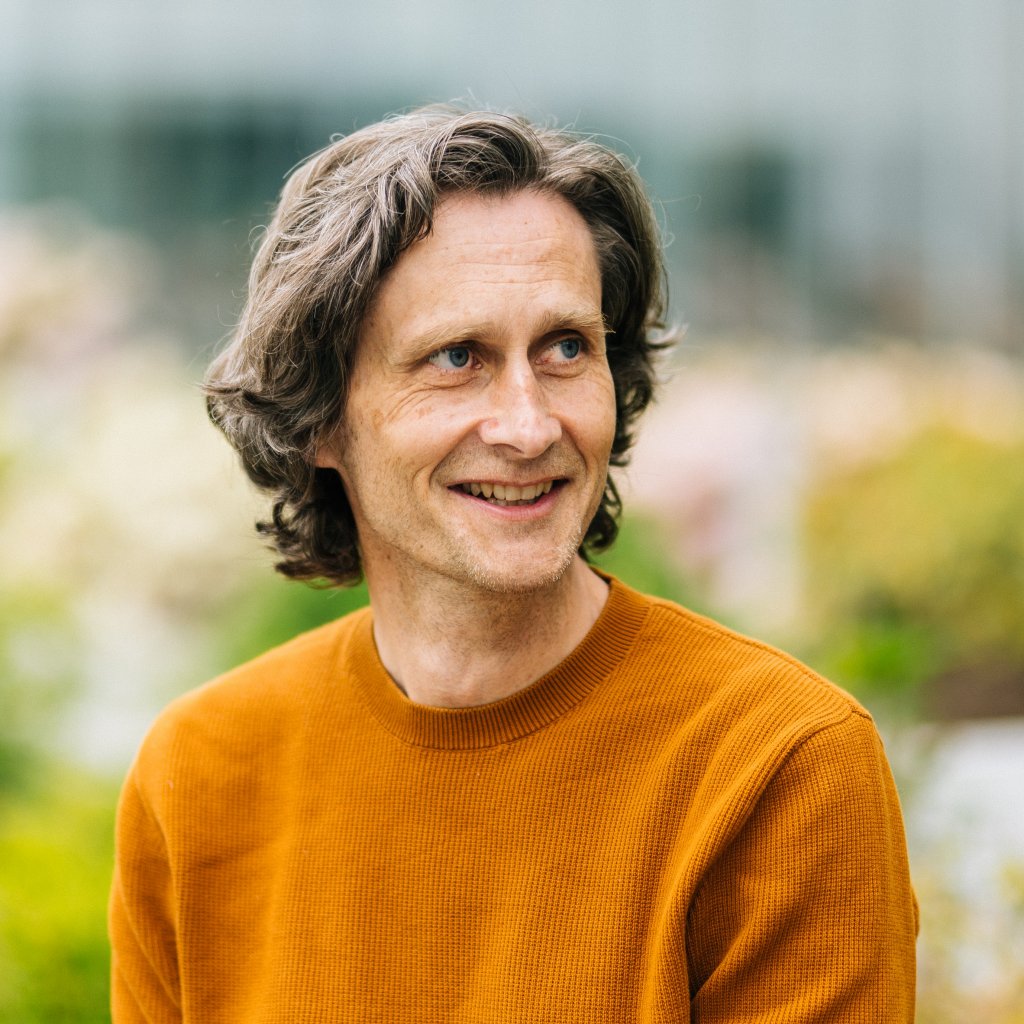
“One universal model would have been ideal, but there are so many differences in the lithology that it’s very difficult to make it work. Troll might have 7 different lithologies, while Johan Sverdrup has 20. We have to do it this way to increase the accuracy of the model."
Harald Eggen
When the Rocky theme finishes playing and the model is fully trained, the GOC can start using it in their day to day.
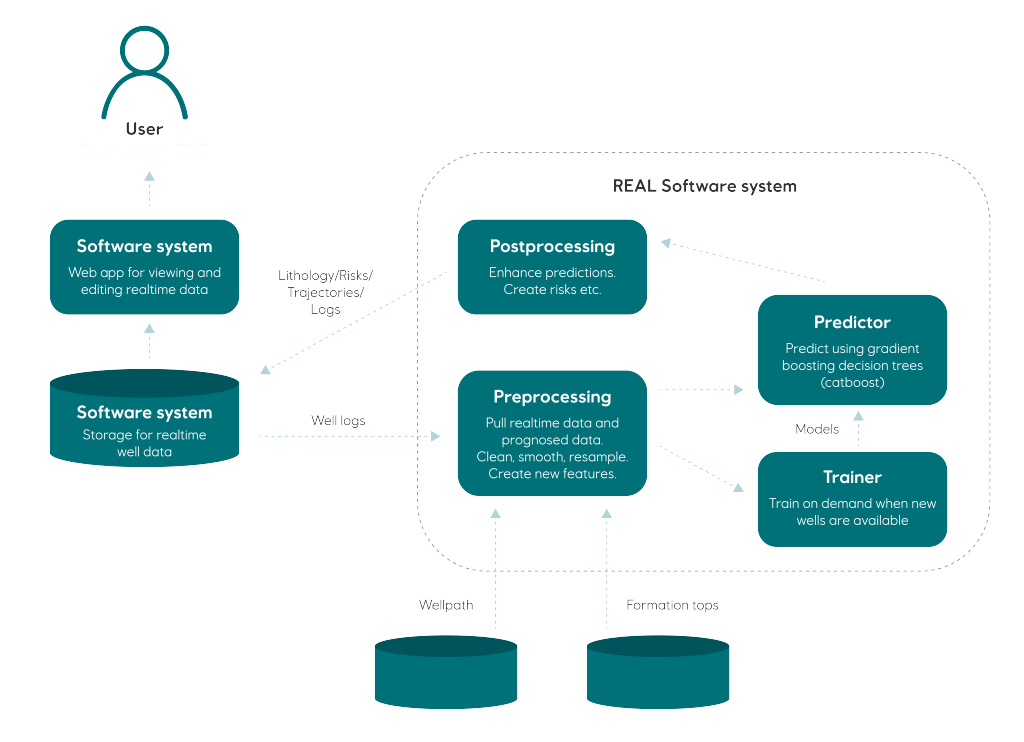
Joining the geology fan club
It isn’t just the machine learning model that gets to benefit from the domain knowledge of geologists - the entire team do! With Linn and Rune having been part of the team since the start, they’ve been teaching their ways to the others.
Either when they’re working together in the day to day or through a week-long course on geology - or on trips to the Pyrenees to study rocks!
“I have to admit that before I started on REAL, I thought “how could anyone be interested in this?”,” Li laughs.
“But in the middle of the project I got so into it! You can see how these different curves behave and from that you know what kind of rock or fluid you’re drilling in - it’s just so cool,” she adds.
Haoyuan Zhang, Hao among us friends, didn’t have much experience in geology either - but explains the close collaboration has been a key part in REAL’s success.
“Without the geologist’s help, the model wouldn’t have become as accurate as it is today. They’ve also helped us to better understand the end user and their needs. Getting to work on something that has such an impact is really rewarding."
Haoyuan Zhang
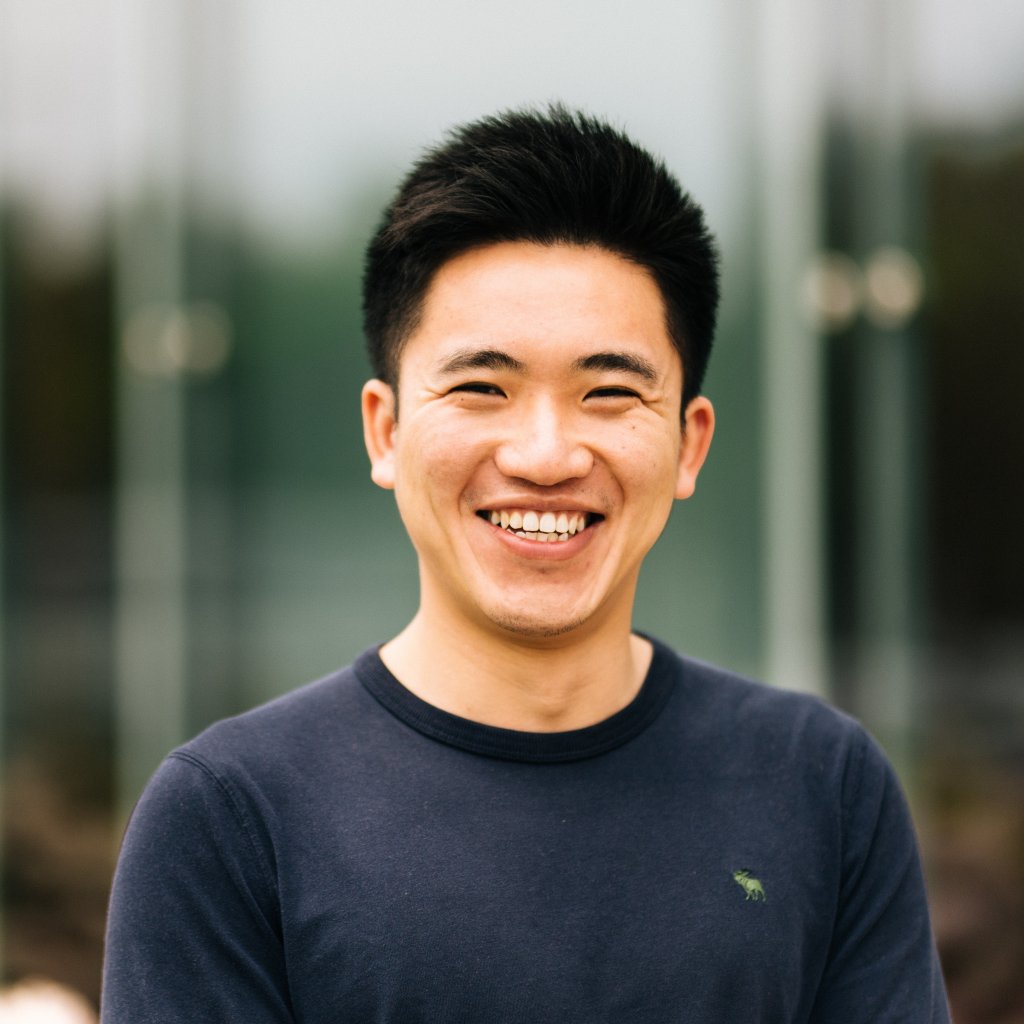
The trinity of drilling a well
When drilling a production well, geologists look at a variety of logs for information. Combinations of these log measurements can be used to define/interpret the lithology, in addition to porosity, water saturation, permeability and fluid type.
Three important ones are radioactivity, resistivity and porosity:
Formation natural/gamma radiation:
Different types of rock emit different amounts and spectra of natural gamma radiation. In particular, claystone/shale usually emit more gamma rays than other sedimentary rocks, such as sandstone, coal or limestone.
Resistivity:
A measurement of how strongly a material, in our case the rock and/or the fluid in the rock pores, resists electric current. The resistivity log is fundamental in formation evaluation because hydrocarbons do not conduct electricity while water does. Clay minerals and a few other minerals also conduct electricity.
Porosity:
A measure of the void spaces in a material. The main tools for porosity measurement while drilling are density and neutron, in addition there is acoustic and NMR tools.
Between a geologist and a rocky place
So, who are the two geologists who have been teaching and working together with our developers? It’s time to meet the fabled Linn Arnesen and Rune Tendenes Kristiansen!
Both Rune and Linn have the same background, but Rune worked for an extended period on the service provider side of drilling operations. That means he has an extensive knowledge of the different equipment used as well as the data types.
They don’t just teach the team about data and geology, they also come up with a variety of suggestions for what REAL needs.
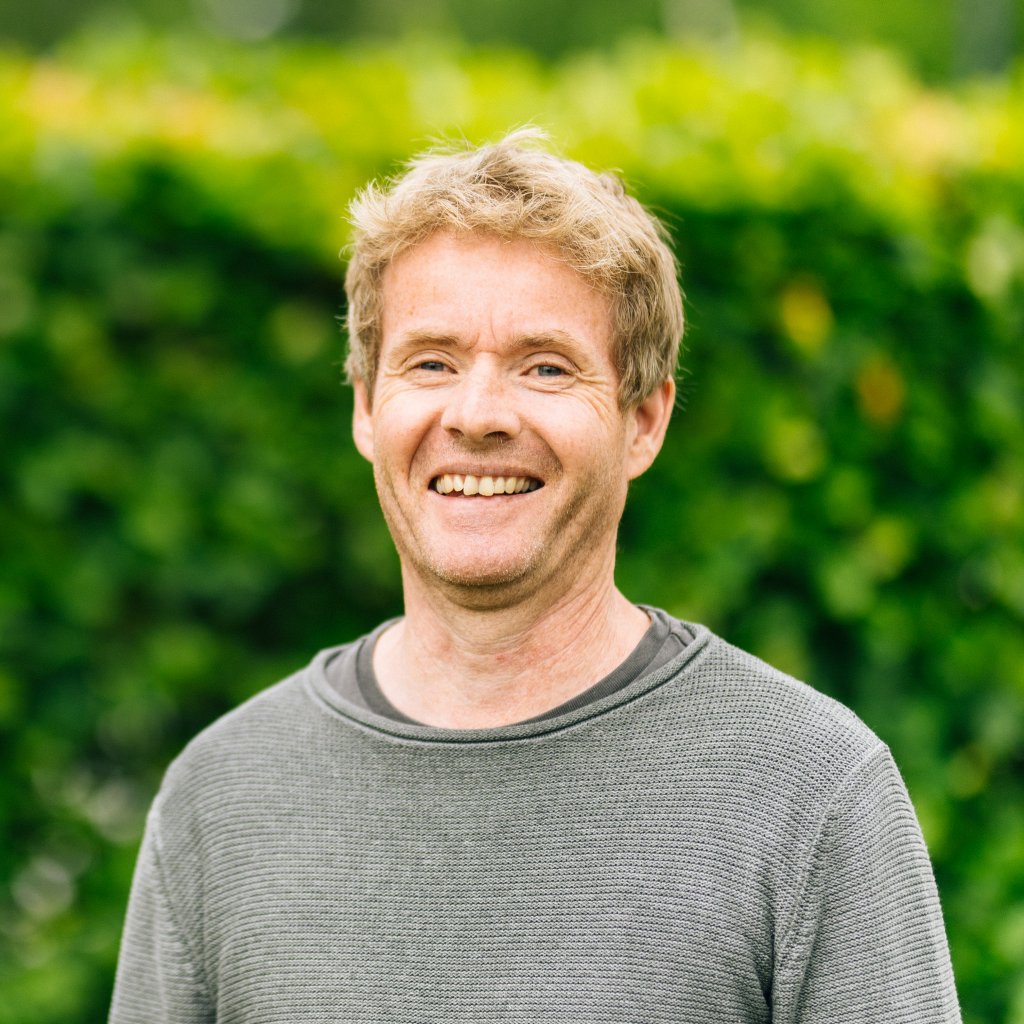
“When we see what these developers can do, we hardly have any problems coming up with more ideas for things we would like to do. REAL is one piece of a big puzzle, but it’s a piece that hasn’t been so accessible previously."
Rune Tendenes Kristiansen
Avid Loop readers may remember Linn from the story about CUILLIN, a machine learning network that analyzes images of rock cuttings. She’s one of the people who came up with the original idea for REAL.
“When I was working on CUILLIN together with these incredible developers, I figured that they could help more of our dreams come to life. And they have!” Linn laughs.
The team working on CUILLIN was part of the REAL pilot, and since then new minds have come and gone. They’ve all contributed to further improving our drilling operations. And make no mistake about it, these drilling operations are far from simple.
“Drilling a production well is about the same as being a dentist and performing surgery with a tiny straw - on a patient that sits five floors below you. That makes it crucial to have interpretations of data that are as consistent as possible, which REAL helps us achieve.”
Linn Arnesen
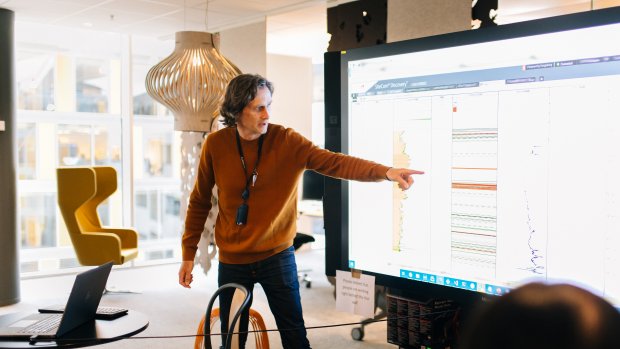
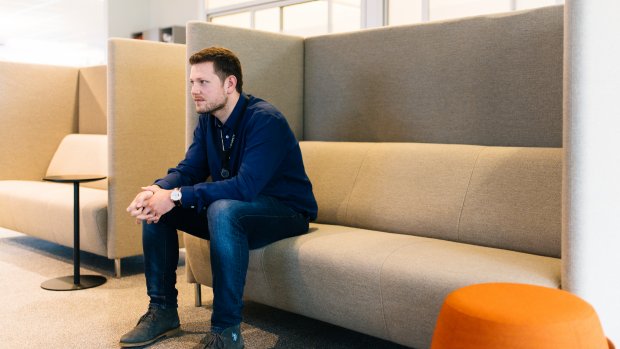
The longest well
We recently finished drilling the longest well on the Norwegian continental shelf. The well is found at Troll and is 10,042 meters long!
At the heart of it all
When Li and Hao left the project in early 2021, two new developers were ready to hop on: Morten Fredriksen and Fredrik Mellemstrand.
Morten tells us that one of the most rewarding aspects of the work is all the feedback they get from end users - and being able to work on something as tech-focused as REAL.
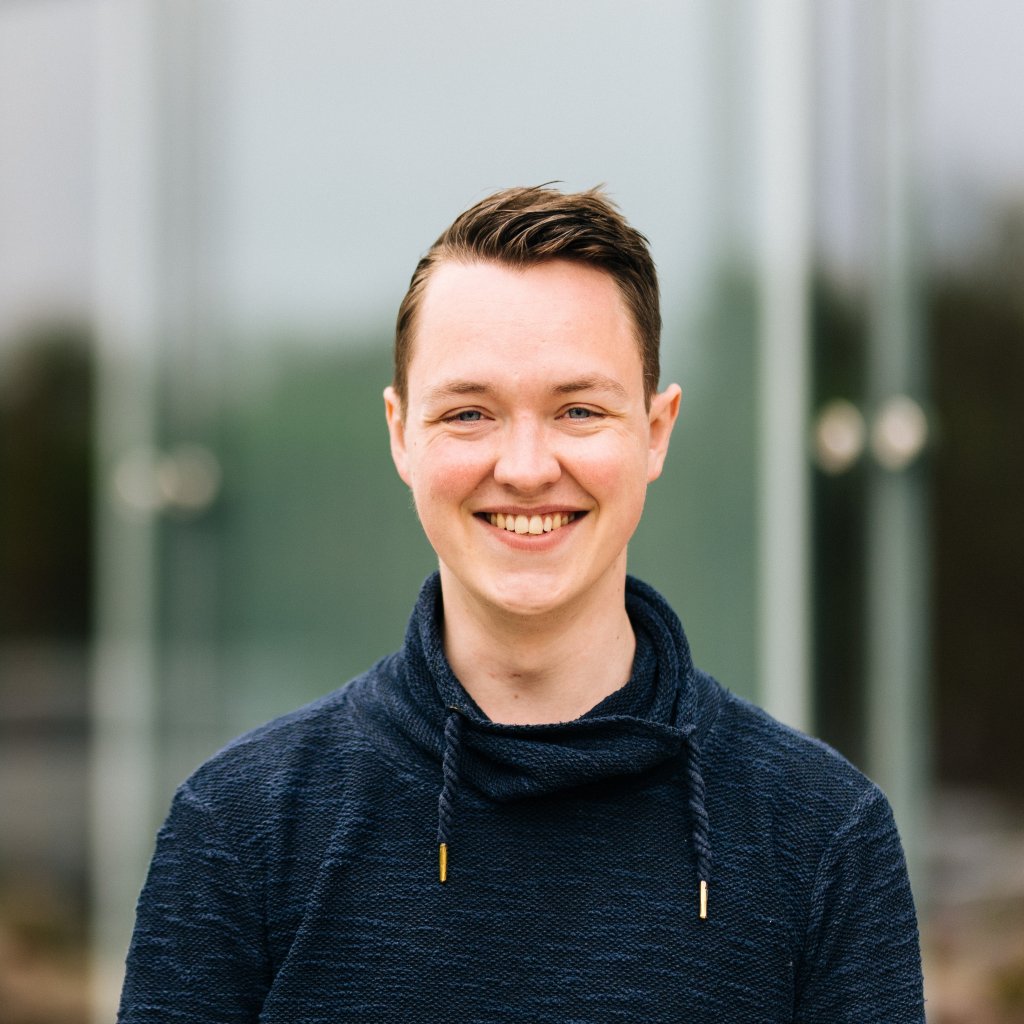
“We collect well data from sensors and try to make it into something with value rather than just 1’s and 0’s. That’s all the while we’re at the very heart of Equinor’s energy production even though we’re in IT."
Morten Fredriksen
Morten is fresh out from his studies and recently joined our Equinor graduate program, but that doesn’t mean he doesn’t have a say in development:
“When we get a task to change or add something, it’s up to me to figure out the best way to do it. We have a lot of say in what tech to implement, which is a lot of fun. That doesn’t mean I’m left all alone though, and I’m lucky to have these experienced developers in the team to learn from,” Morten smiles.
Fredrik has more experience under his Equinor-belt but joined the team earlier this year. Maintenance and developing REAL further are at the top of all their to-do-lists.
“REAL is in use 24/7 and we’re dealing with live data so there’s always a challenge to face and solve. Interpretations are constantly running and being presented to the geoscientists at the GOC. That’s what makes all of this so exciting.”
Fredrik Mellemstrand
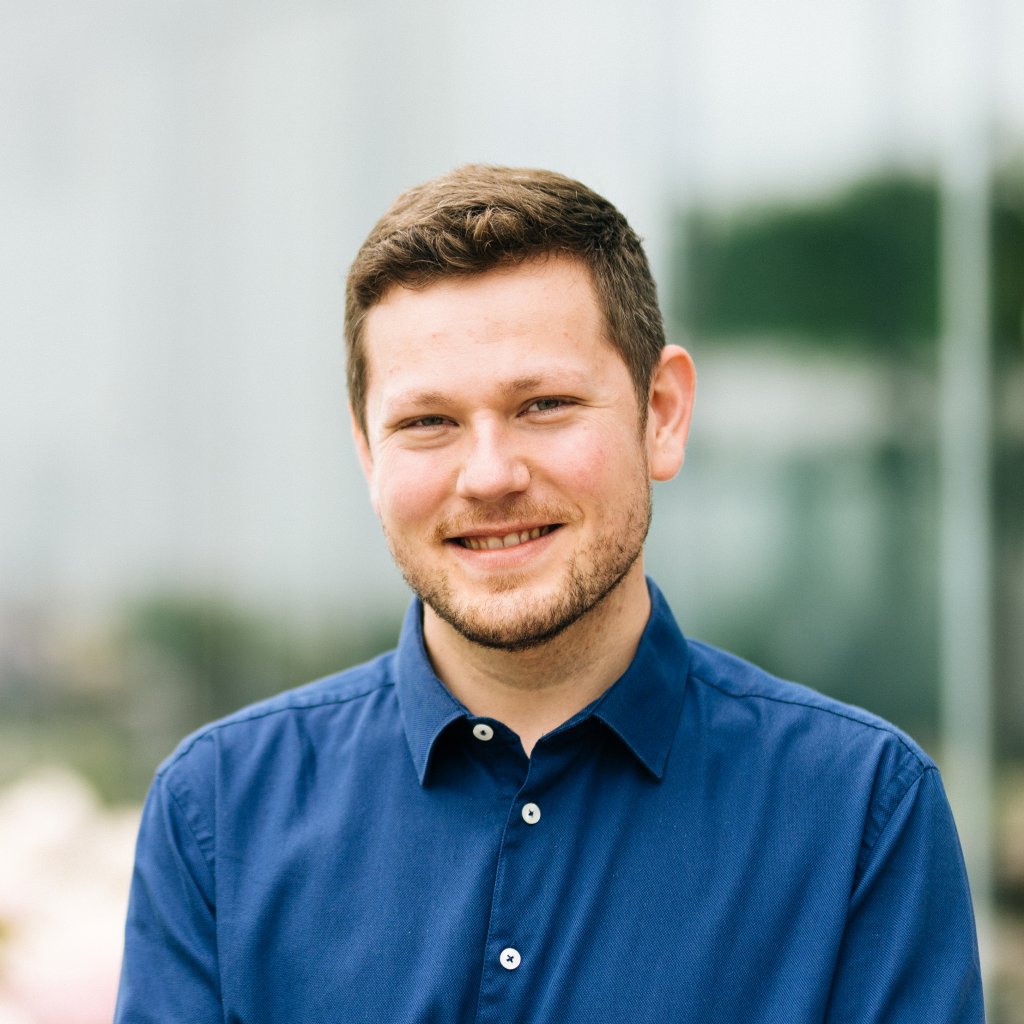
Naturally, development is far more than just maintenance. The team is also looking into possibilities of making sure their model can keep on learning and evolving.
“As of now, we’re only training the model when we’re adding a new field. Being able to train the model continuously using live data would be an interesting addition to the work. That way, we could use new data together with REAL’s interpretations to further improve on our model,” Harald explains.
Here at Loop, we’re not in the business of predicting what the future holds for REAL. However, what we do know is that if you’re interested in all thing's software from Equinor - you need to subscribe to our newsletter. Then, an email will find its way to you as soon as we publish a new story. We won’t spam you and we promise to make it an interesting read.
Until next time, stay safe and take care!
People
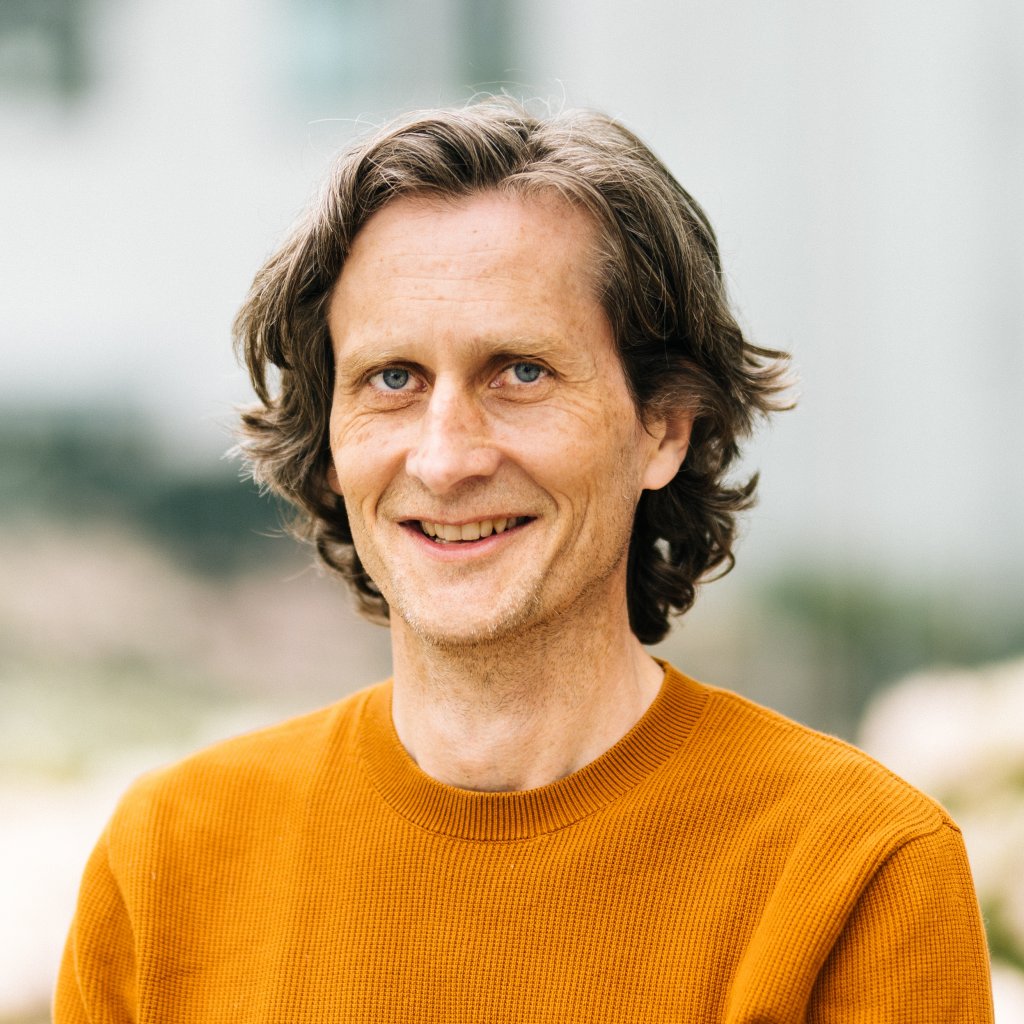
Harald Eggen
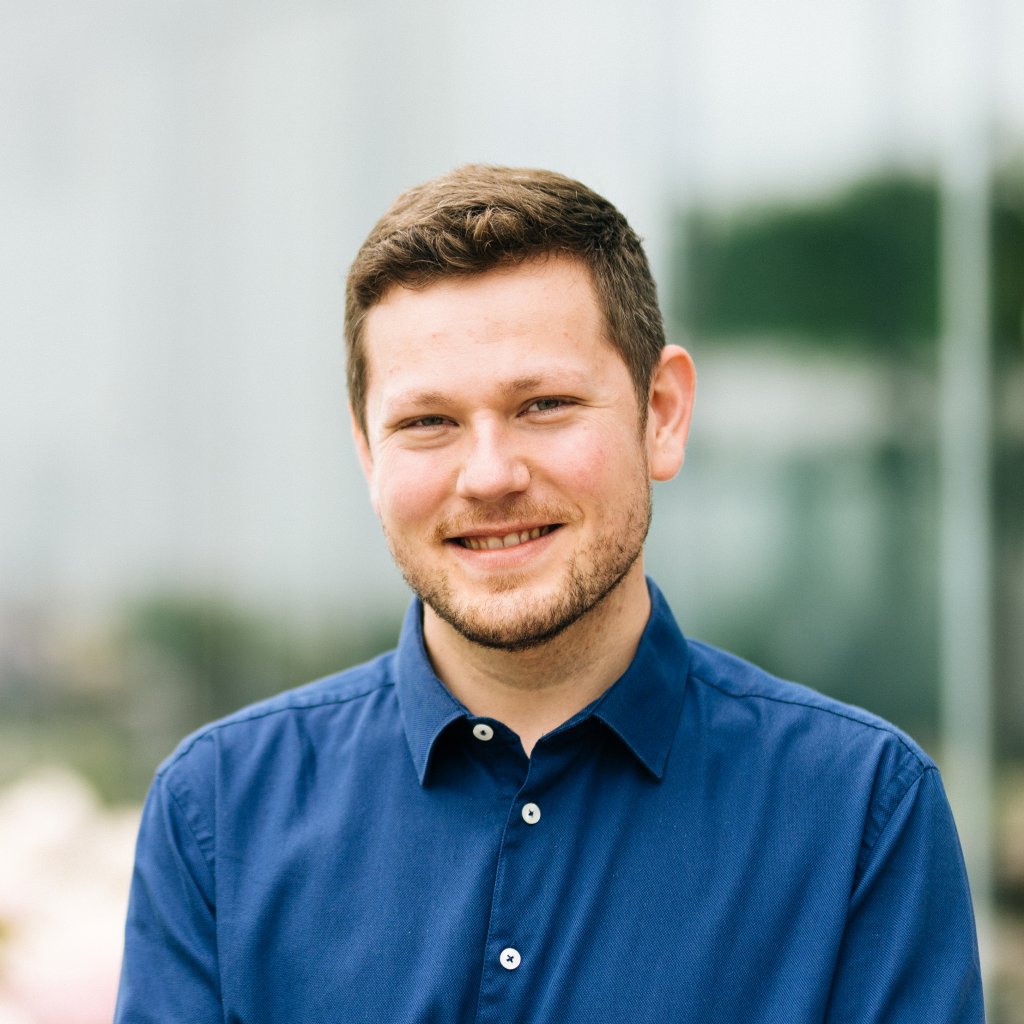
Fredrik Mellemstrand
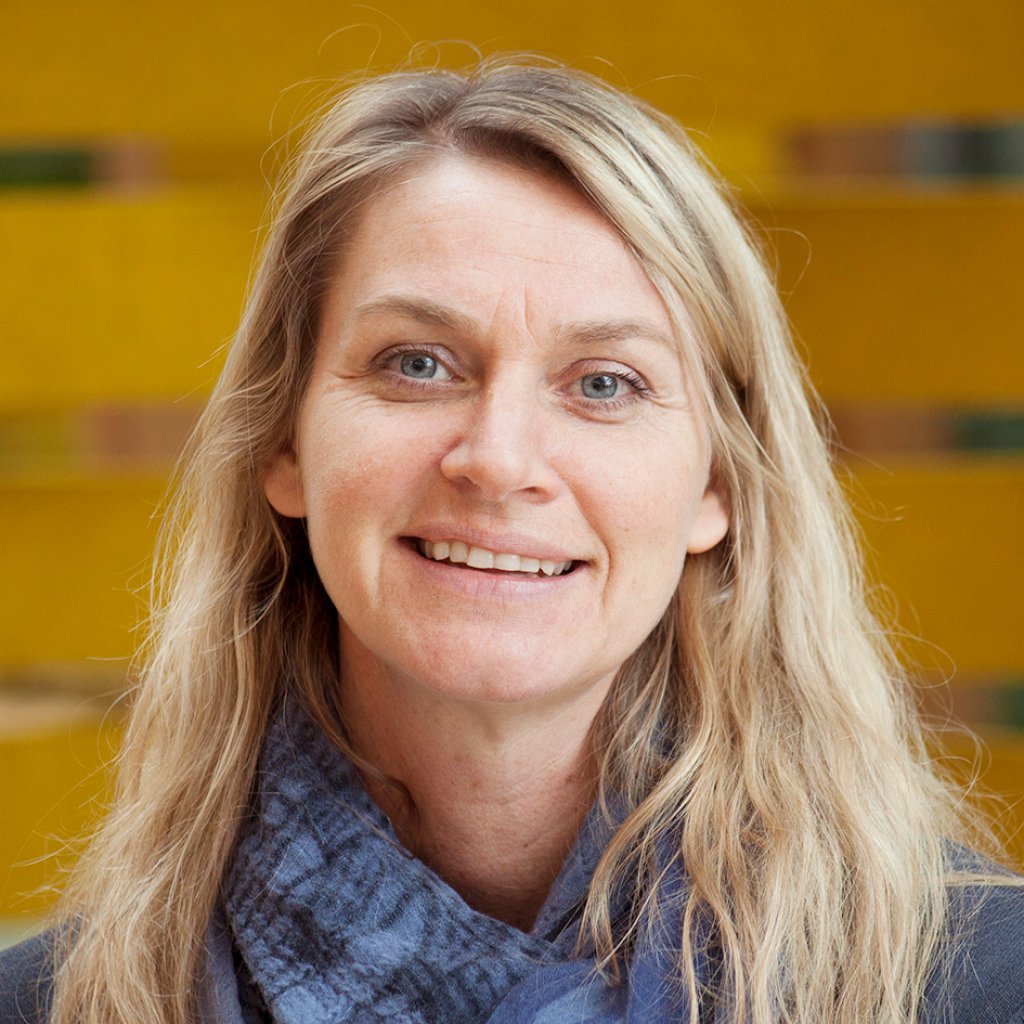
Linn Arnesen
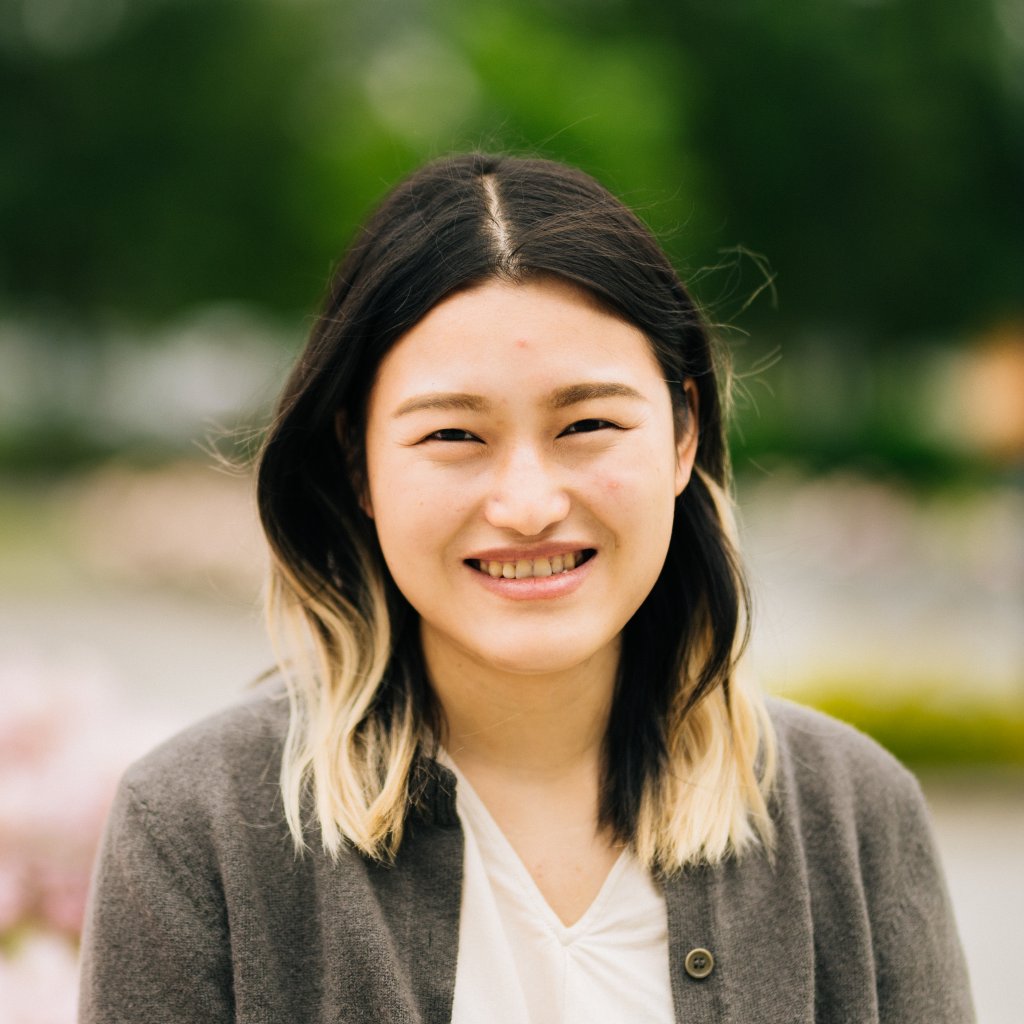
Li Deng
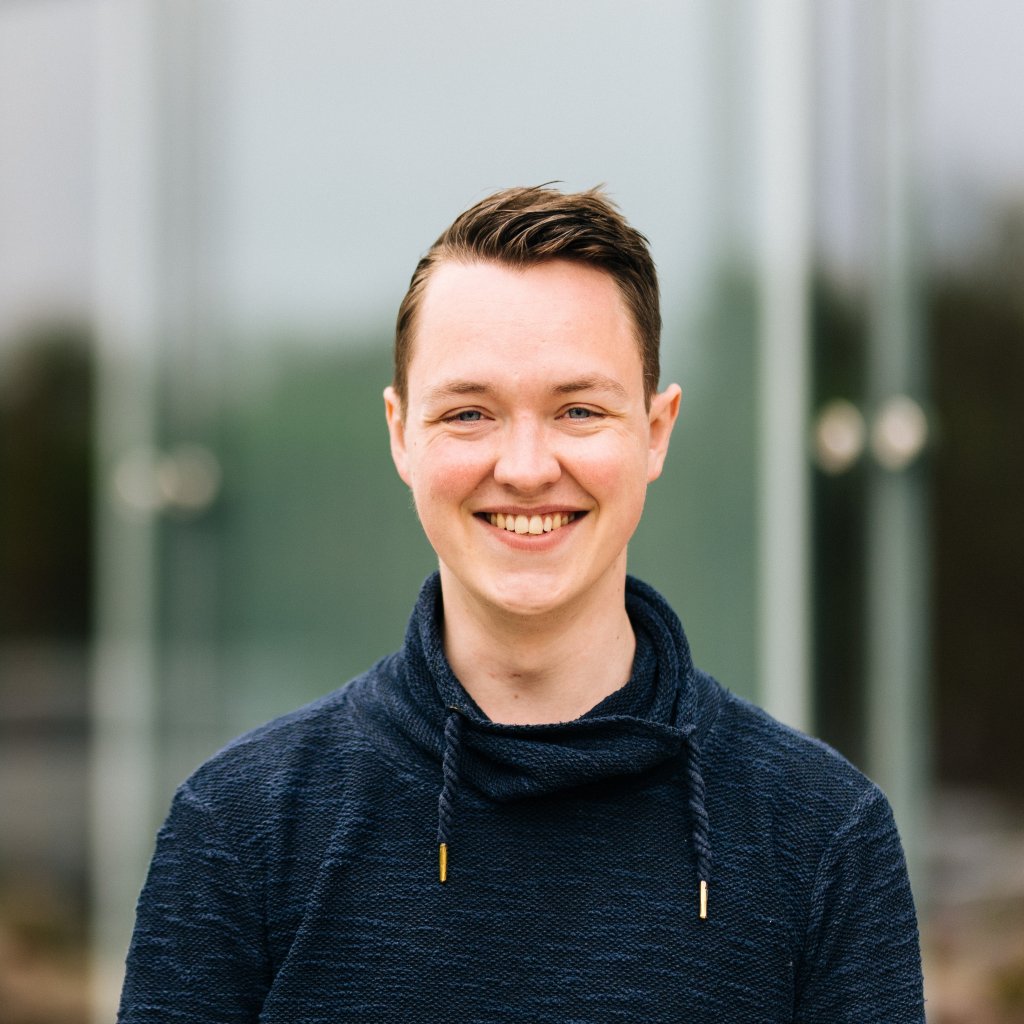
Morten Fredriksen
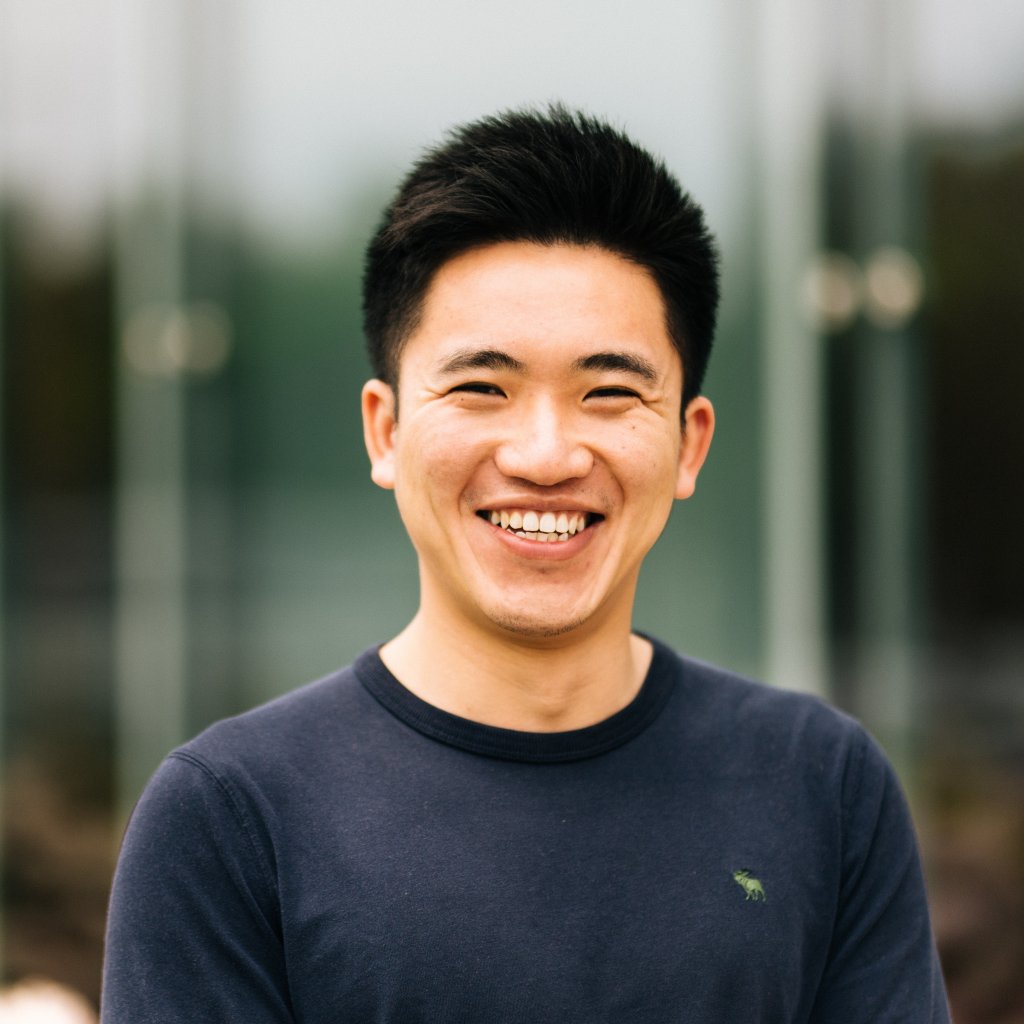
Haoyuan Zhang
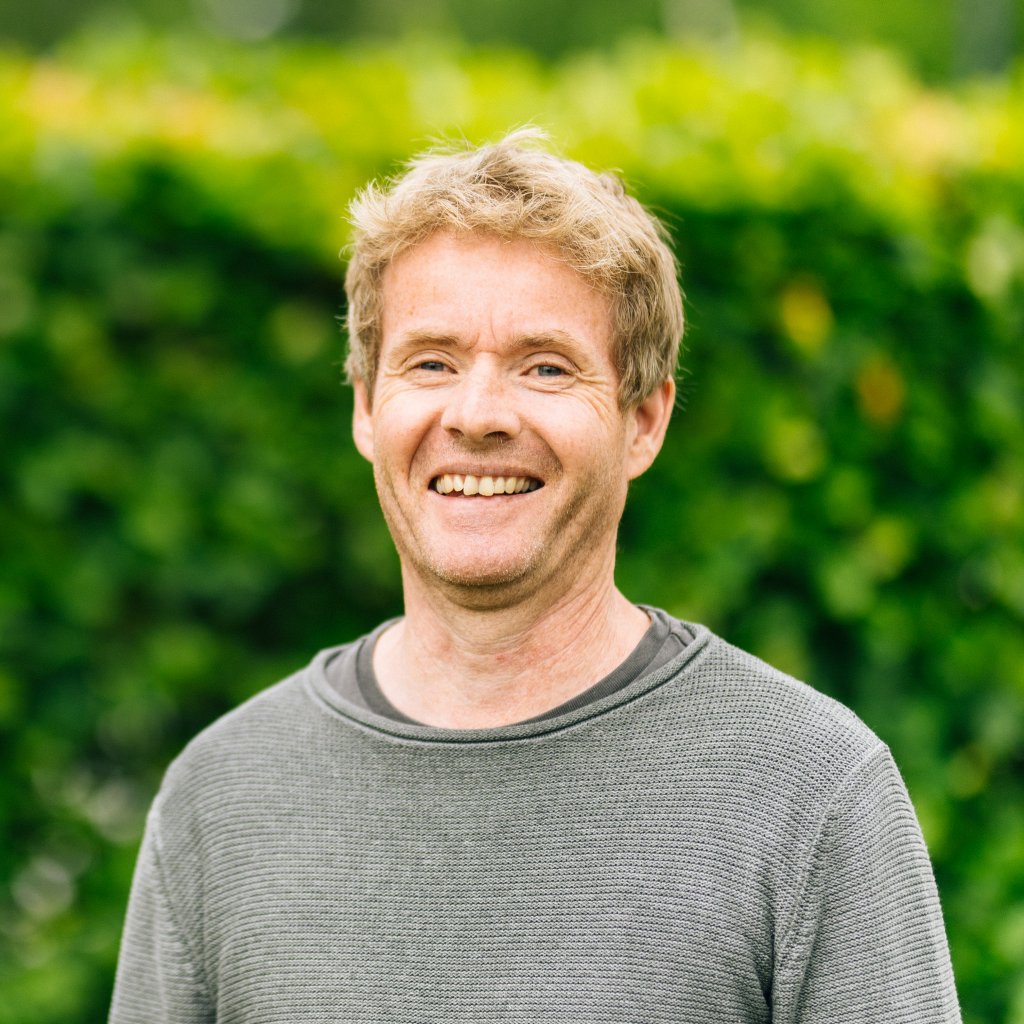
Rune Tendenes Kristiansen
Related stories
Showing stories for