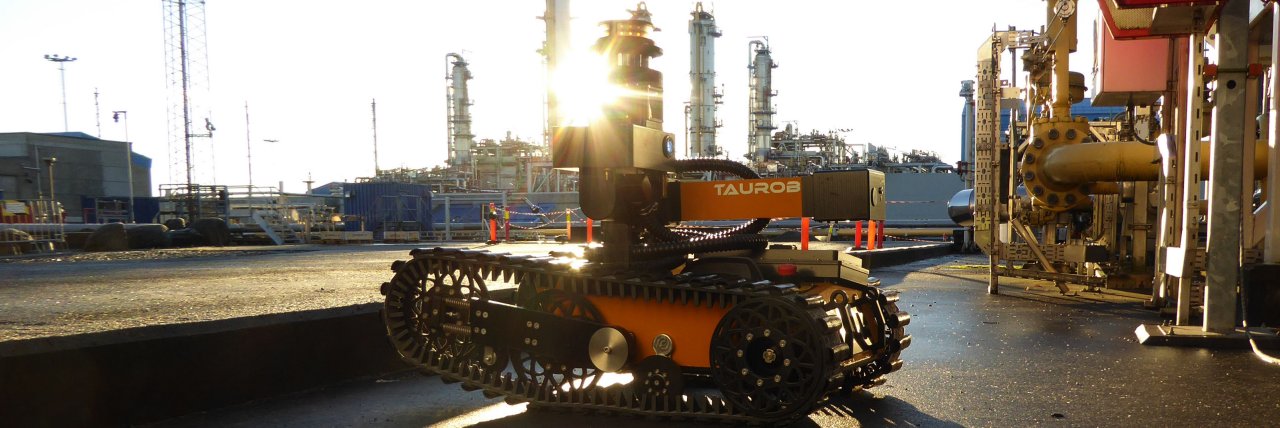
Our first autonomous robot
Here’s the tale of the first autonomous robot heading offshore, and the software development that’s making it come to life. Let’s meet Taurob.
For quite some time already, us humans have instructed robots to take care of tasks we either can’t do or tasks we don’t necessarily want to do. And like the little circular buddy doing your vacuuming, we’re aiming to have self-driving robots help us with a variety of tasks offshore.
One of these robots is Taurob - named after it’s manufacturer. But what’s so special about this Taurob robot? It’s simply that it has the required classification to operate in what’s called an ATEX Zone 1: process areas where gasses are more likely to be present. This means that Taurob doesn’t create any sparks that can ignite potential gasses.
“The plan for Taurob is to have it on unmanned installations and function as our eyes, ears and hands. If an incident occurs, then we can use the robot to quickly get an overview of the situation.”
Anders Røyrøy
Anders has been working with robotics in Equinor for almost 15 years. He is currently part of the team working on the Taurob robot, based in Research & Technology.
“An important reason behind our work with robotics is to not expose personnel to any hazardous work,” Anders says.
Robots can help us avoid the four D’s of work: dangerous, distant, dull and dirty. Letting robots help us with these types of tasks doesn't just improve safety, they also improve efficiency, economy and the quality of work.
Focusing on safety and security
Taurob comes complete with hardware and software from the manufacturer, but integration with our own systems is being done by software developers in Equinor.
Arnt Erik Stene is one of the software developers working on making sure the robot, nicknamed Taurob after its manufacturer, will be up to the task. He tells us that the biggest difference when developing code meant for a robot is that the code has an effect in the physical world.
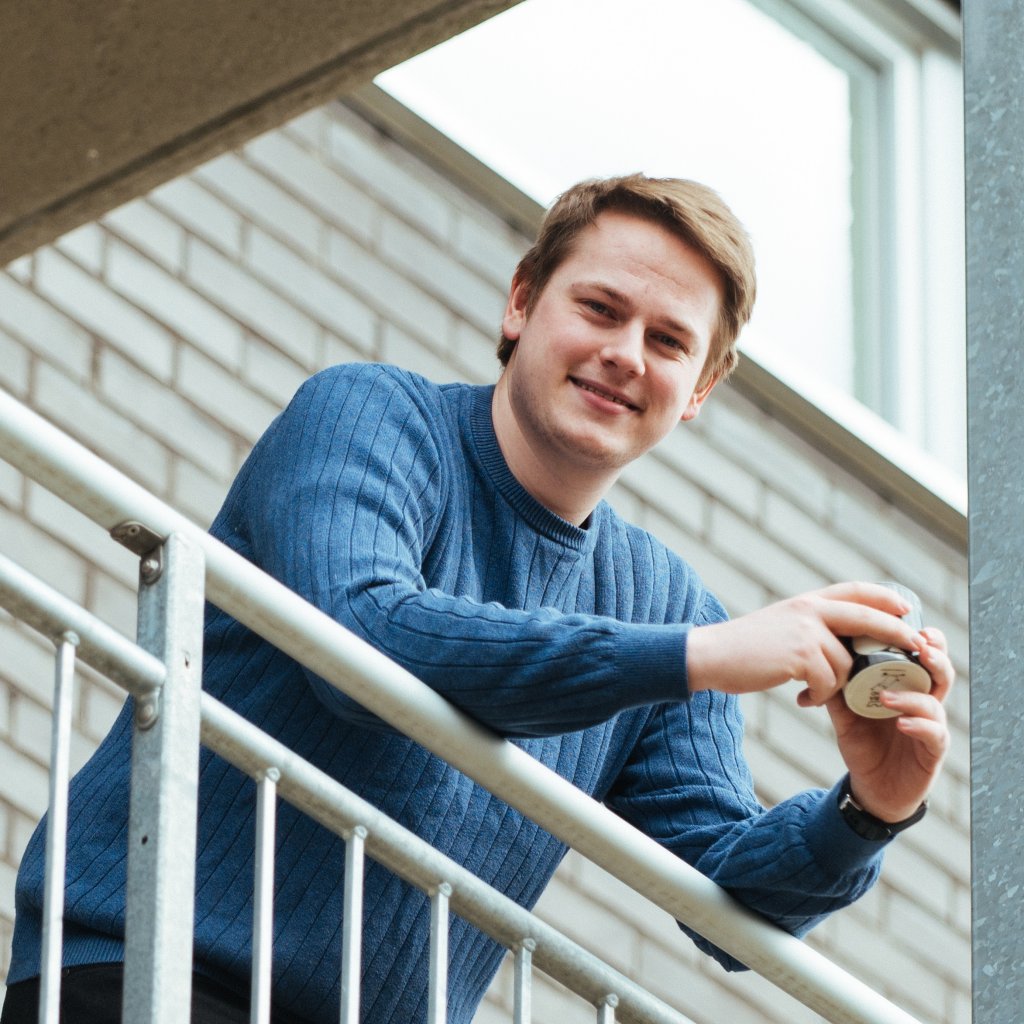
“We have to make sure that our code doesn’t result in the robot doing something unexpected, which requires a lot of testing. There’s added focus on safety and security when we’re developing since we didn’t build the actual robot.”
Arnt Erik Stene
Since the robot itself has been created by someone else, all the code the team writes and implements goes on top of an already existing layer of code.
But what does all this testing actually mean? And how do they do it? Time to find out!
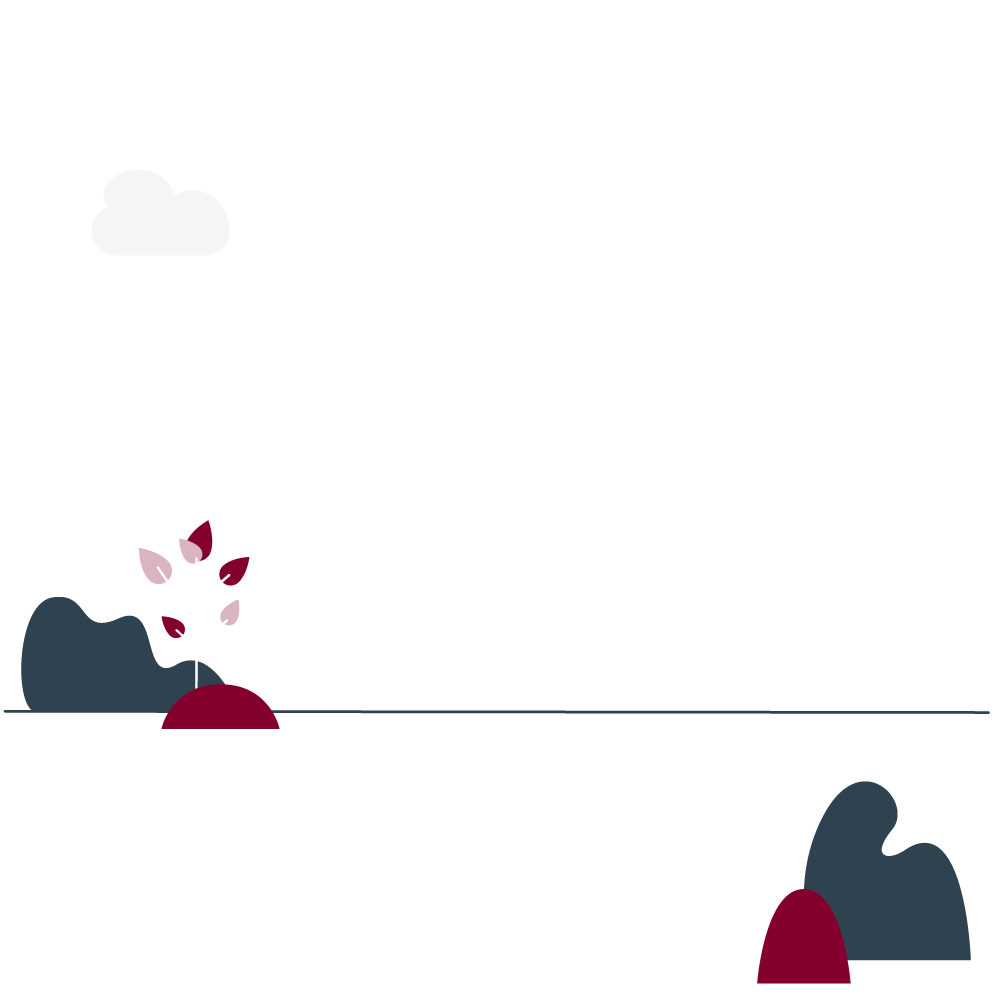
Taurob at a glance
- Autonomous robot produced by Taurob
- Scheduled to help with inspections and maintenance on unmanned, low-manned or normally unmanned offshore installations
- ATEX Zone 1 certification robot
- First offshore test is set to be the Johan Sverdrup field center
- Developed in collaboration with Total and OGTC
Welcome to the simulation
The team was fully assembled in August of 2020, and have since spent their time working on the software for Taurob. One of the main parts of software development has been running simulations and getting a feel for how the robot would act in the real world.
“We’ve used a physics simulator together with 3D models of both the robot and our facilities to run simulations. This allows us to test everything we need without driving an actual robot,” Arnt Erik explains.
In short, a physics simulator is basically a tool that provides an approximate emulation of the real world in a virtual environment.
“Let’s say the robot is driving around the simulation and has to pass a corner. If the robot tries to cut the corner, the simulated physics ensures that the robot reacts as if it hit it. Without the physics simulated the robot would simply pass straight through,” developer Øystein Barth Utbjoe explains.
“These simulations let us see if the robot is capable of maneuvering around on its own and how it reacts to its surroundings,” Øystein adds.
Thanks to the Equinor digital twin Echo, we have 3D models of many of our assets. Among them is Johan Sverdrup, which is set to be Taurob’s first test site offshore.
“Having these models to use in simulations means that we can simulate Taurob in environments it will actually work in. If something doesn’t work in the simulator, chances are it won’t work in the real world either," Øystein explains.
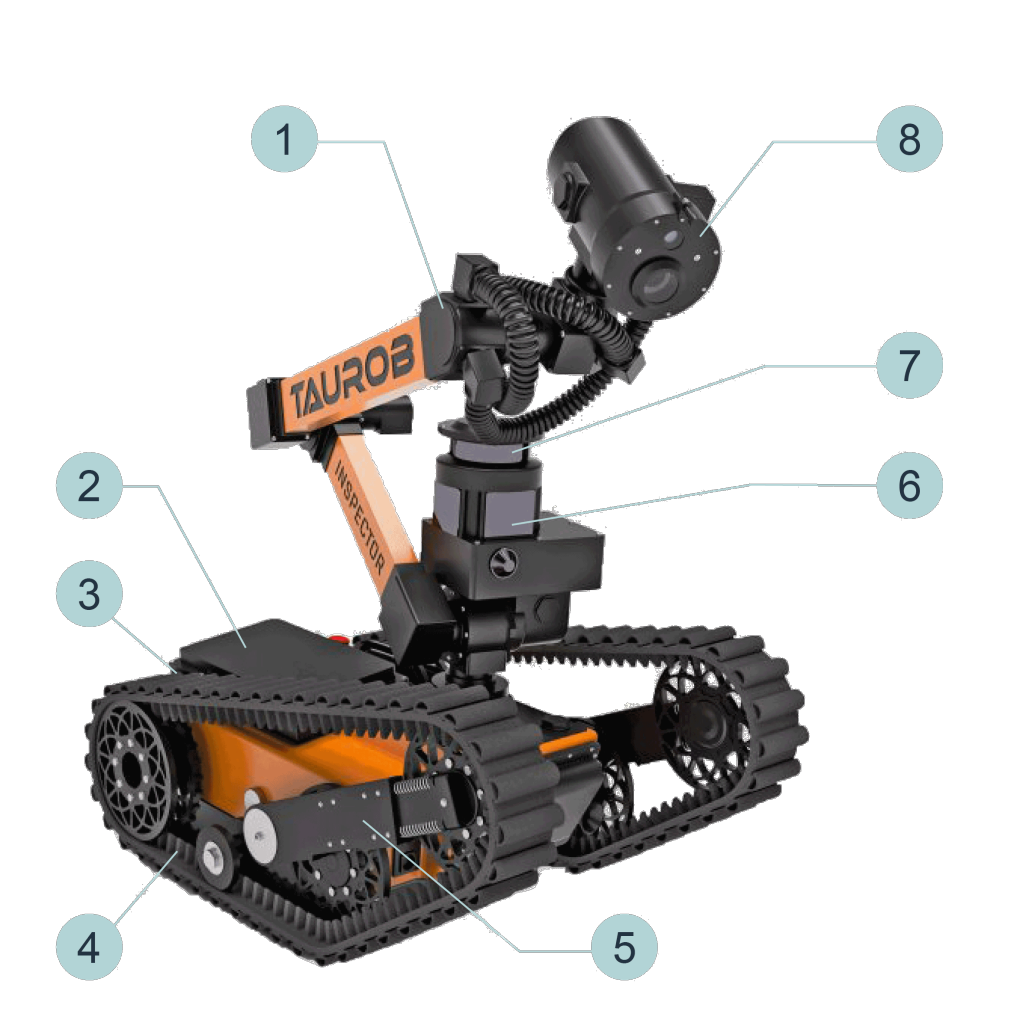
The parts of a robot
- 5 Degrees of freedom arm
- Ruggedized industrial PC, neural processor & safety controller
- 4G/LTE communications
- Optimized track system for industrial sites
- Moveable flippers
- 3D Lidar
- 360° camera
- UHD camera, thermal camera
Testing, one, two, three
Life is more than just a simulation and in November of 2020, the team had the chance to head on out to KLab. That’s our very own testing facility at Kårstø, where they got to see how the robot would do on an actual processing facility.
All three developers got to head down to take part in testing, but due to Covid-19 restrictions they weren’t always there at the same time.
Even though they had been running through simulations, nothing compares to the real thing. This meant they had several “aha moments” at KLab - and as expected, some troubleshooting. One example was the mapping service Taurob uses.
“Taurob uses a map service to pinpoint itself on a map and we had assumed that it worked one certain way. Then, when we discovered it worked another way we had to troubleshoot and make changes to the software from our home office,” developer Einar Skiftestad Ueland tells us
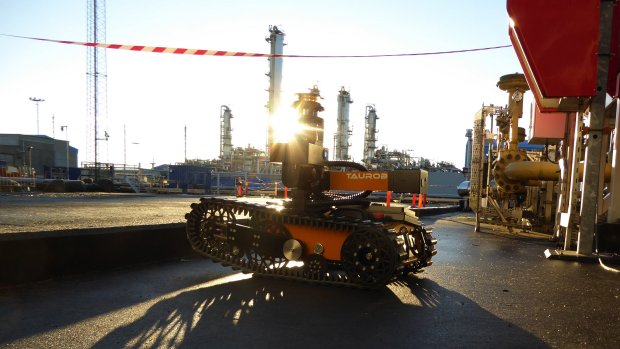
Their days consisted of a whole lot of testing and troubleshooting both within the team and together with the people behind the robot itself through Teams. While you might think that not finding any bugs is a good thing, that’s not true for developers.
“If you ask me, finding bugs is a positive thing - because it means we’re checking and testing the right things. I would be very surprised and slightly worried if everything worked as intended on these first tests.”
Øystein Barth Utbjoe
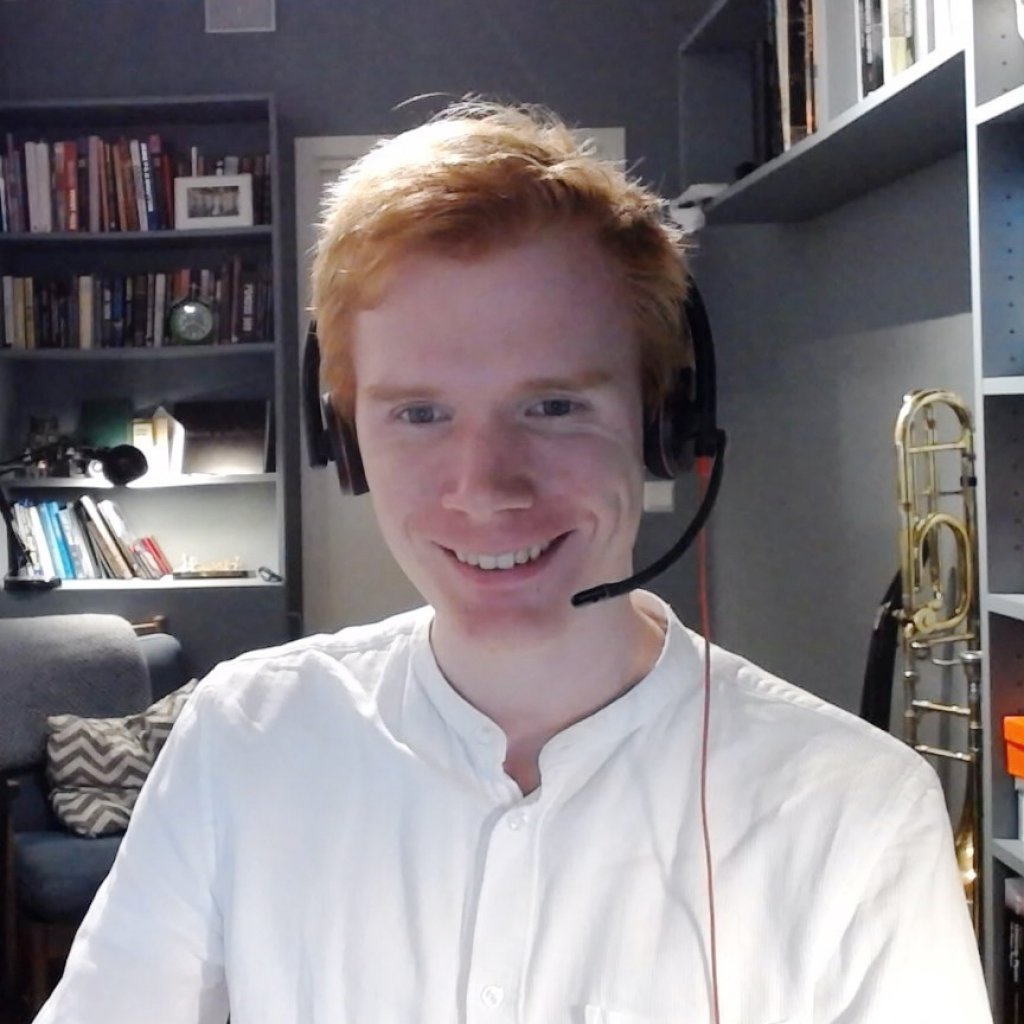
“It only took a couple hours from us discovering bugs to fixing them. I think a lot of that was due to having spent so much time on simulations,” Øystein adds.
Stay in the Loop
Getting a first-person experience
Both Arnt Erik and Øystein tell us that getting to visit the test lab at Kårstø has been a highlight.
Our Kårstø testing facility, KLab, has a dedicated crew that’s always ready to help out during testing. If you have any questions they have answers, and if you need anything they’ll get it to you.
“There are a lot of things that need to be done that we wouldn’t have thought of, but the operators at KLab are incredible at what they do and provided us with excellent help," Øystein says.
“Since we’re normally working in an office, we’re never up close and personal with the actual oil and gas production. Kårstø is such a big facility and it was really fascinating to experience the scale of things first hand.”
Arnt Erik Stene
“It was also a change in mindset when we were there. You put the protective gear on, have to call up operators to have them approve our work orders etc. After a while we were able to do more of that on our own, which was very motivating,” Øystein says.
“There’s more to driving a robot on a processing plant than simply bringing your laptop. Testing gave us a better understanding of everything “extra” that’s happening around running the robot,” he adds.
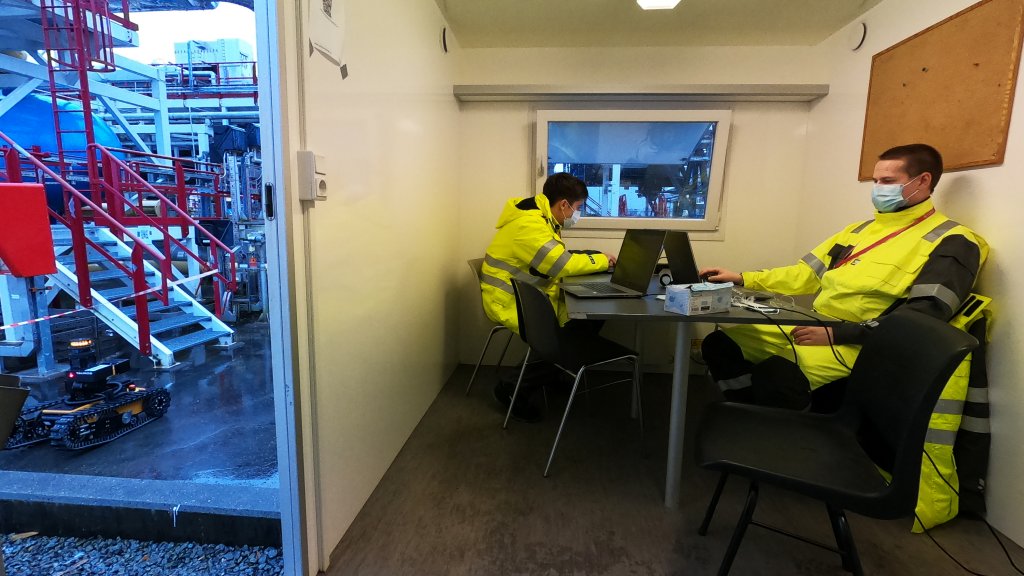
Variety is the name of the game
Getting a robot to drive itself around an offshore installation is only a piece of the puzzle, another key piece is figuring out where to go. For this you need a clear map of where to go and find everything that needs to be found. Thankfully, our Equinor digital twin Echo has got them covered with unique IDs and tags for everything from valves to helipads.
"If the robot is going to inspect 4000 valves on an installation, I wouldn’t want to be the one that has to manually input locations for each one. Since this information is already found in Echo we’ve been working on ways to integrate it with Taurob."
Øystein Barth Utbjoe
The Echo team already has a robotization workflow in place and while some functionality is already available, they’re also working together with the team to figure out what’s needed.
“This variety in the work we do is something I really enjoy. We’re not just developing code, we’re also working with other software development teams and suppliers to see how we can make it all fit together,” Øystein says.
Article continues below photos.
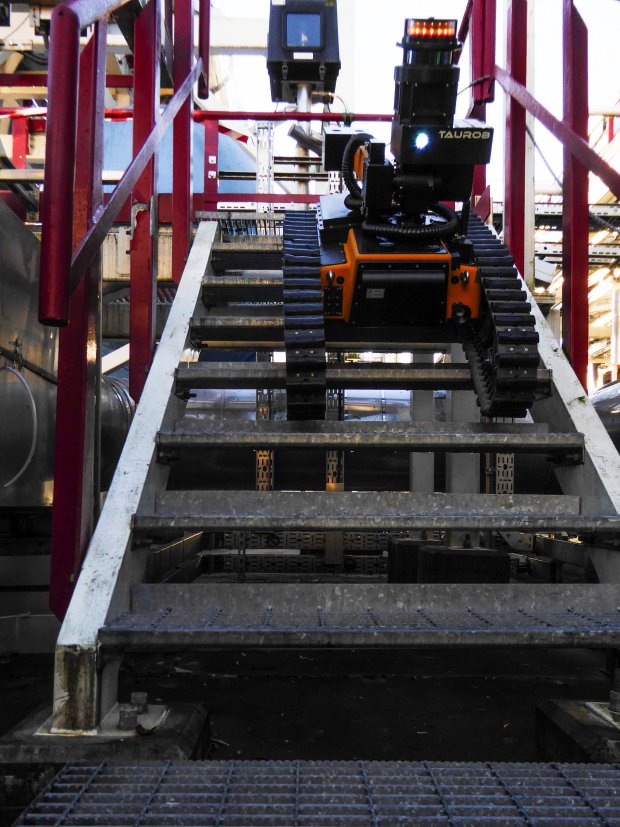
Building a proper foundation
All three of the developers on the team are Equinor graduates and they all come from a background in cybernetics and robotics. Arnt Erik had spent the first part of his time as a graduate in Software Innovation, and was the one with the most experience in software development.
“We introduced agile principles on ways to work, but we also implemented some things designed to increase our competence and the quality of our work. We’re not the most experienced team of developers but we’re aware of that - and working on shaping the best path forward,” Arnt Erik says.
Together with standups, sprints and sprint retrospectives, code reviews and version control are some of the many principles they’ve introduced to the team.
“Focusing on writing quality code which lasts means the work is a lot more rewarding from a developer’s point of view. Our goal is for the solution to be robust and simple, so that it can be further developed by future team members."
Arnt Erik Stene
He’s been leading the team into the craftsmanship world of software development, which has meant correcting minor details along the way to make sure they’re getting things done right. After all, the devil is in the details.
“It didn’t take long until we saw the benefits of being so detail-oriented. Now, doing things the quick and easy way means we do it slower and worse than if we’re being thorough,” Øystein explains.
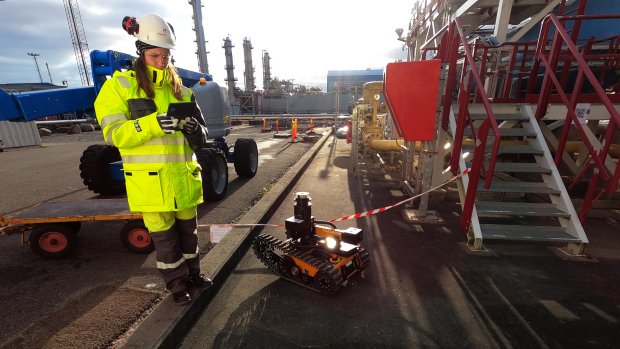
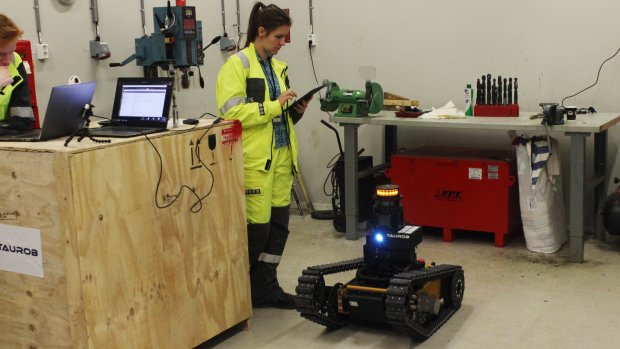
More testing to come
With the first rounds of testing completed, the team is now working on even more testing and simulations.
“Now, we’re working on building upon and improving on what we learned at the KLab test. We have more tests on the actual robot planned and we need to be ready for that,” Arnt Erik explains.
“We’re also working together with other Equinor teams, like Echo, on ways we can make use of them for Taurob,” he adds.
The team will also be welcoming some new members, among them graduates, and Arnt Erik tells us that they’re working on improving documentation in order to make onboarding as smooth as possible in the future.
“We’ve improved a little bit already but we still have a way to go,” he smiles.
And if all goes well, we might be seeing Taurob in action on our installations in the very near future. If you want to stay in the loop on everything software development-related in Equinor, don’t forget to subscribe to our newsletter using the link below.
Until next time - stay safe and take care!
People
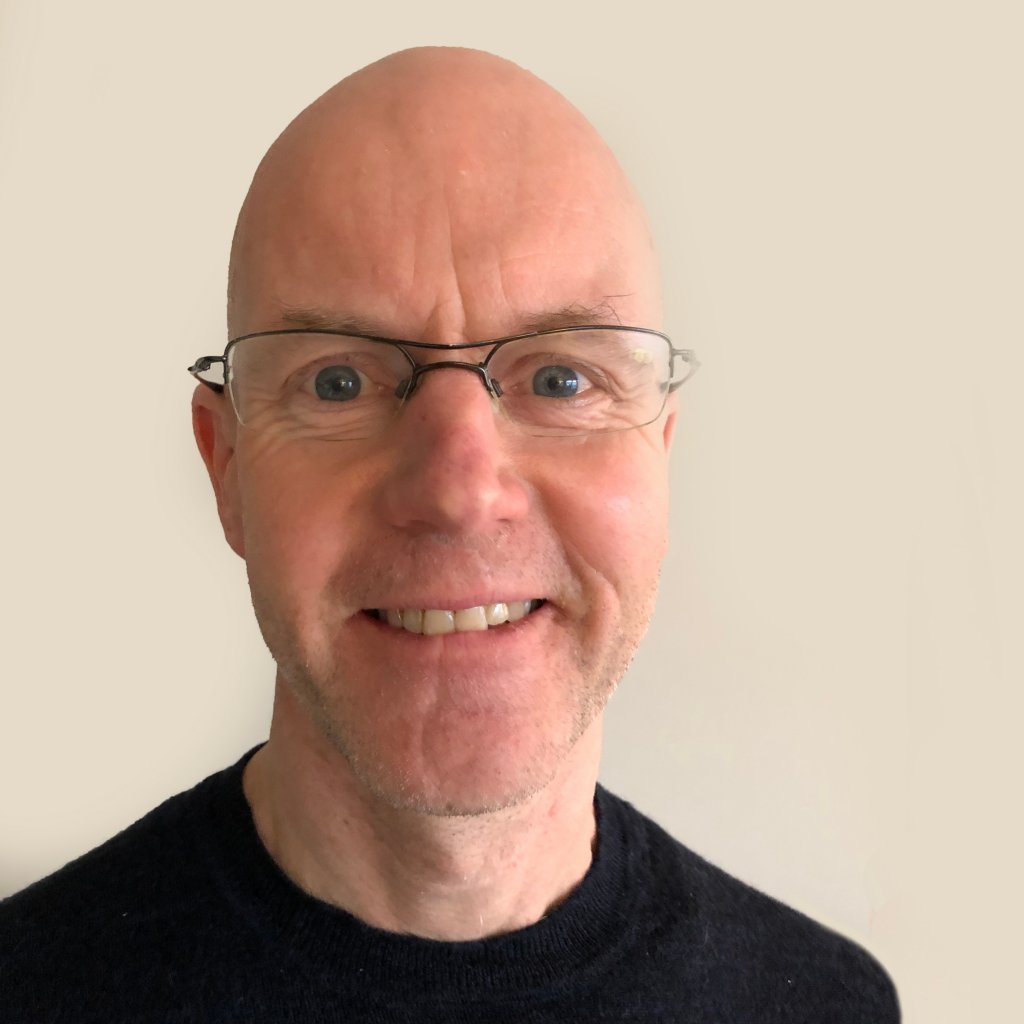
Anders Røyrøy
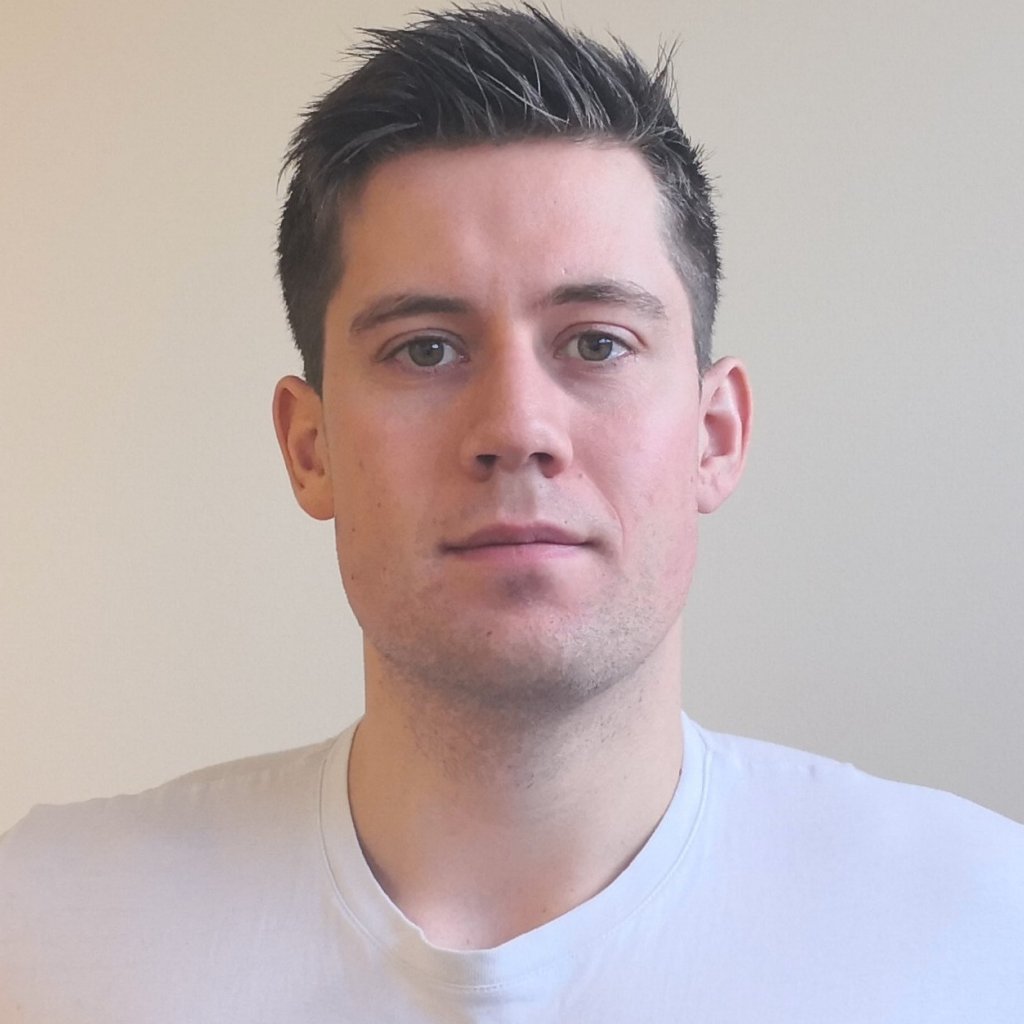
Einar Skiftestad Ueland
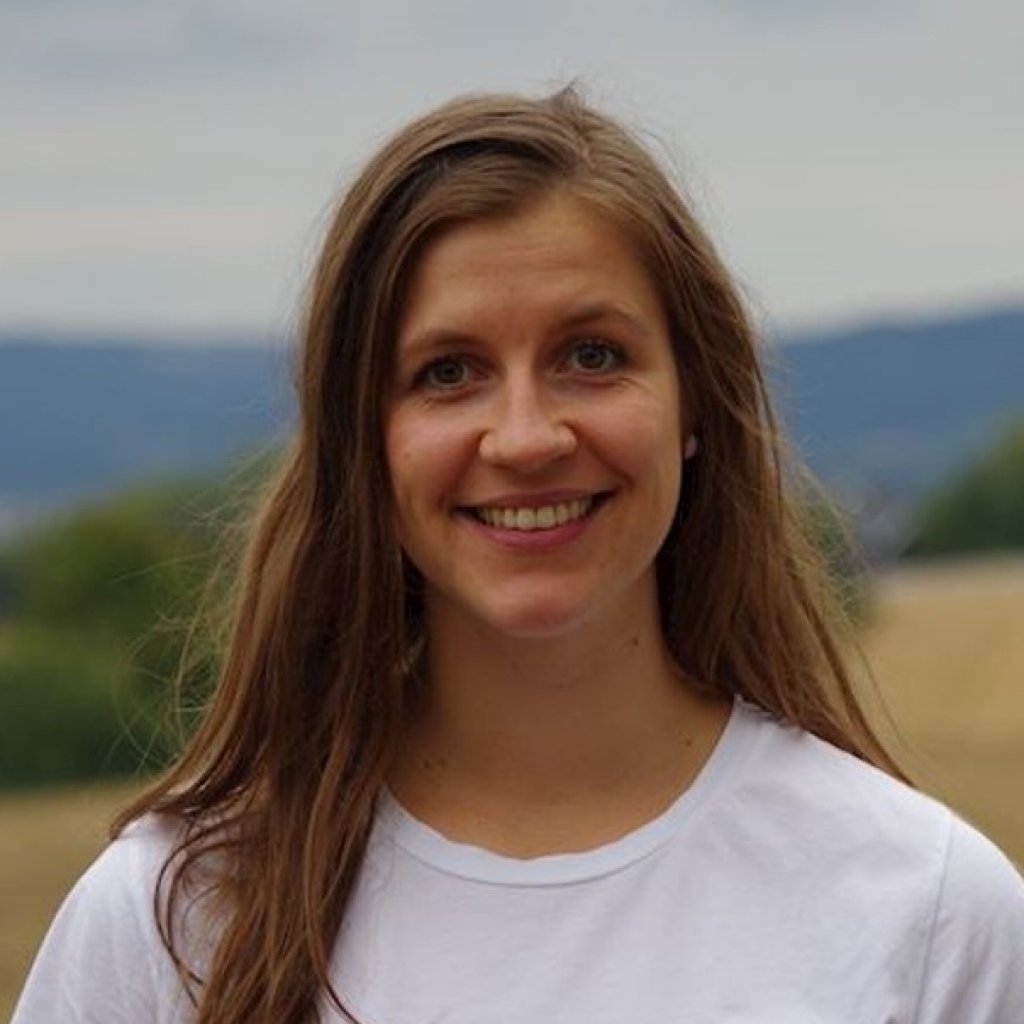
Monica Svensli Glomstad
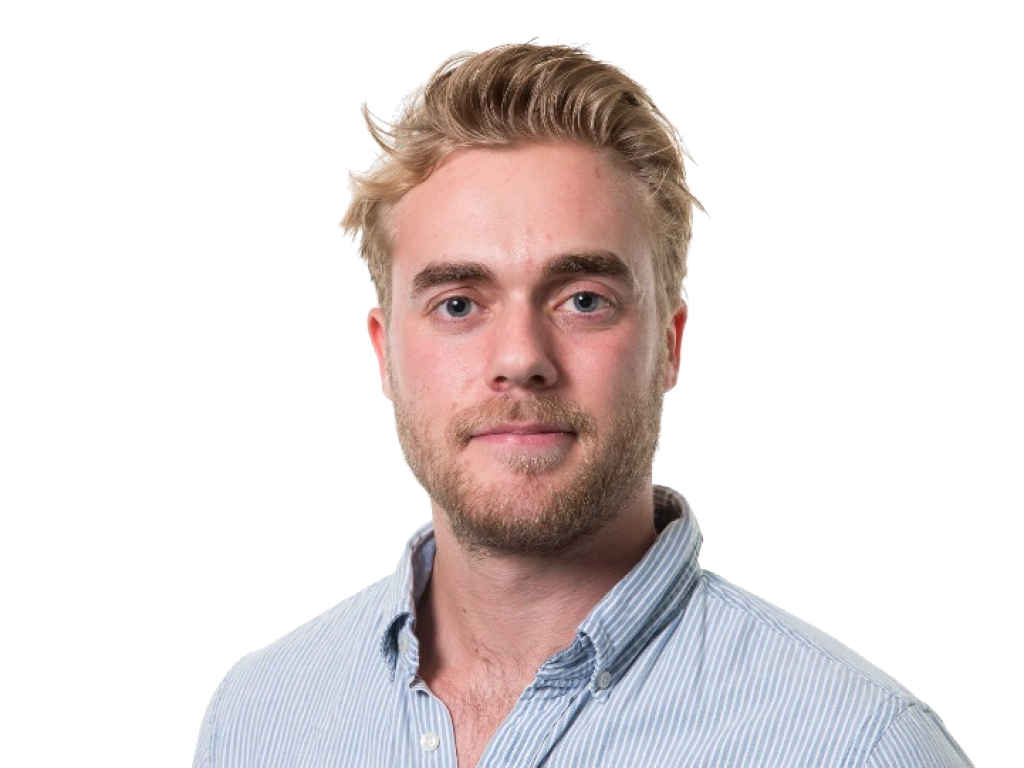
Christian De Jonge
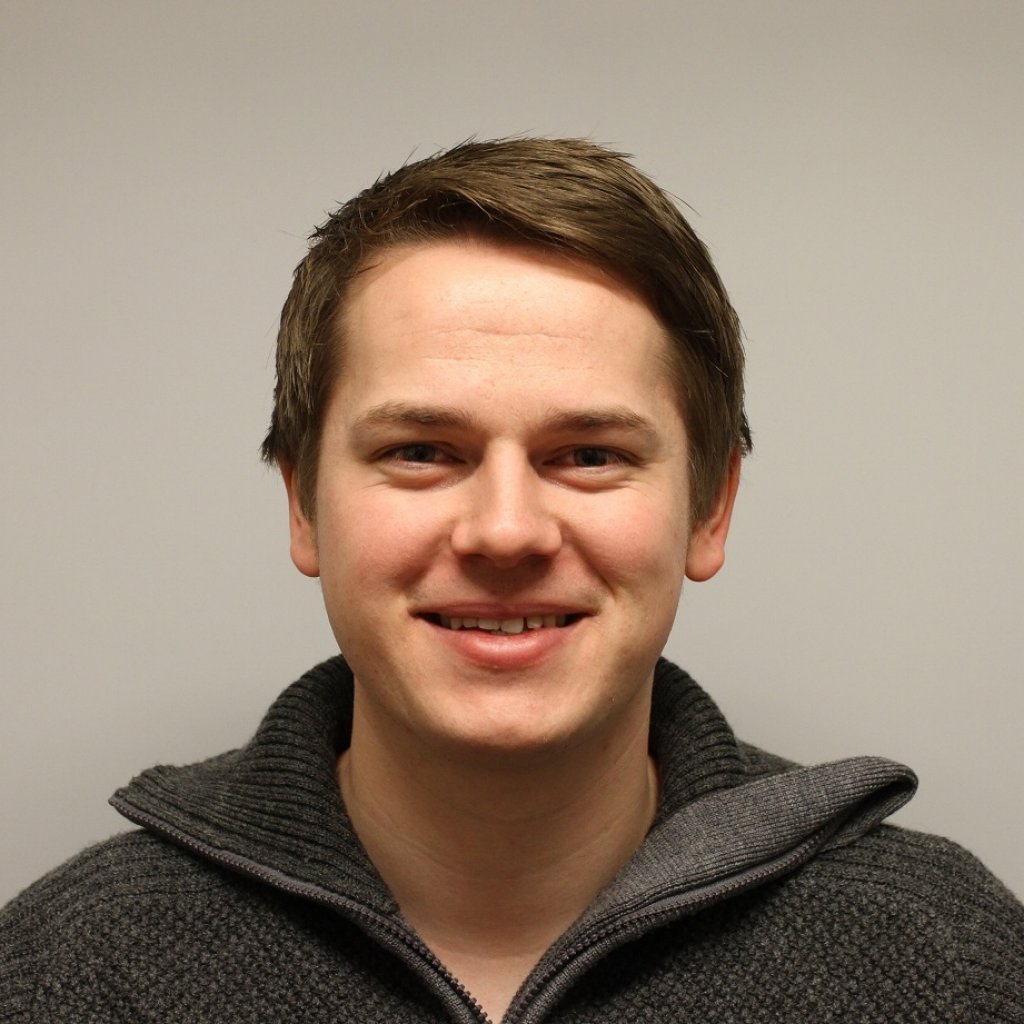
Arnt Erik Stene

Svein Ivar Sagatun
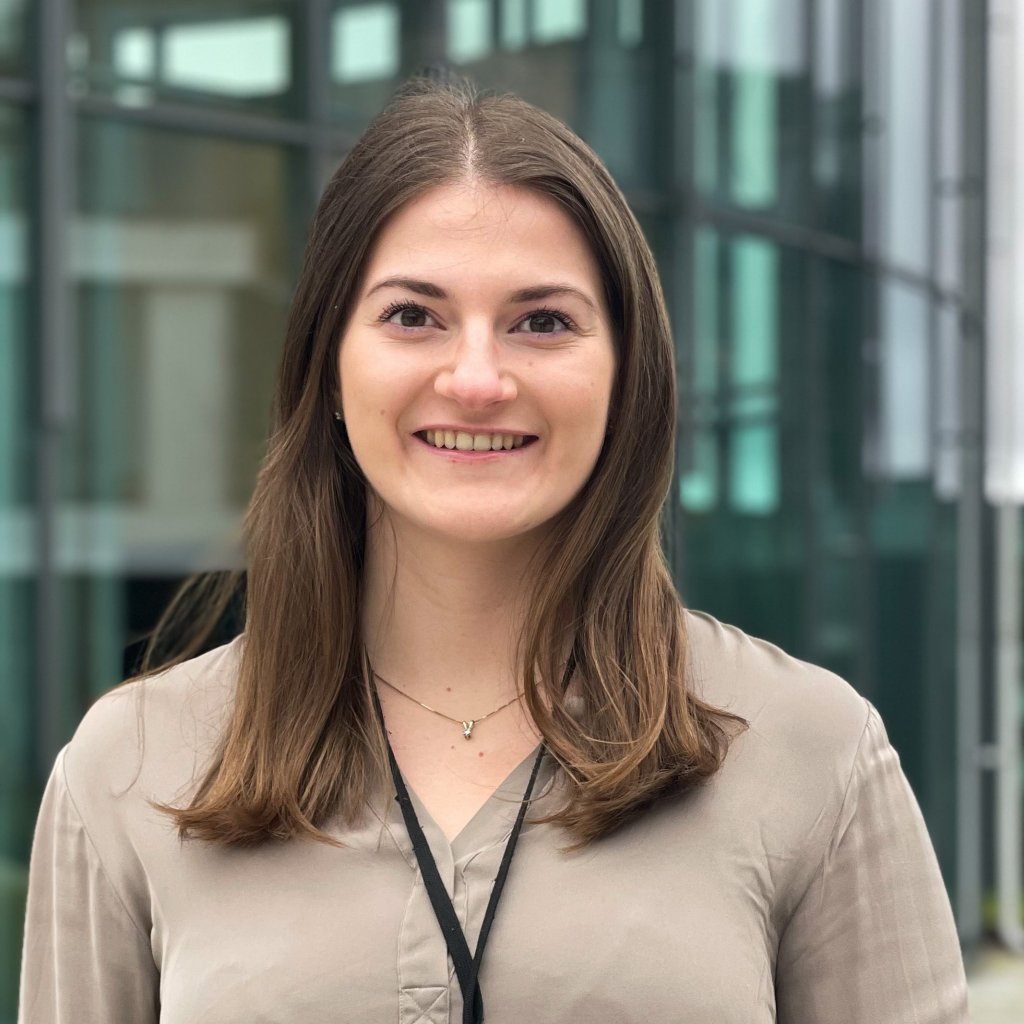
Anette Uttisrud
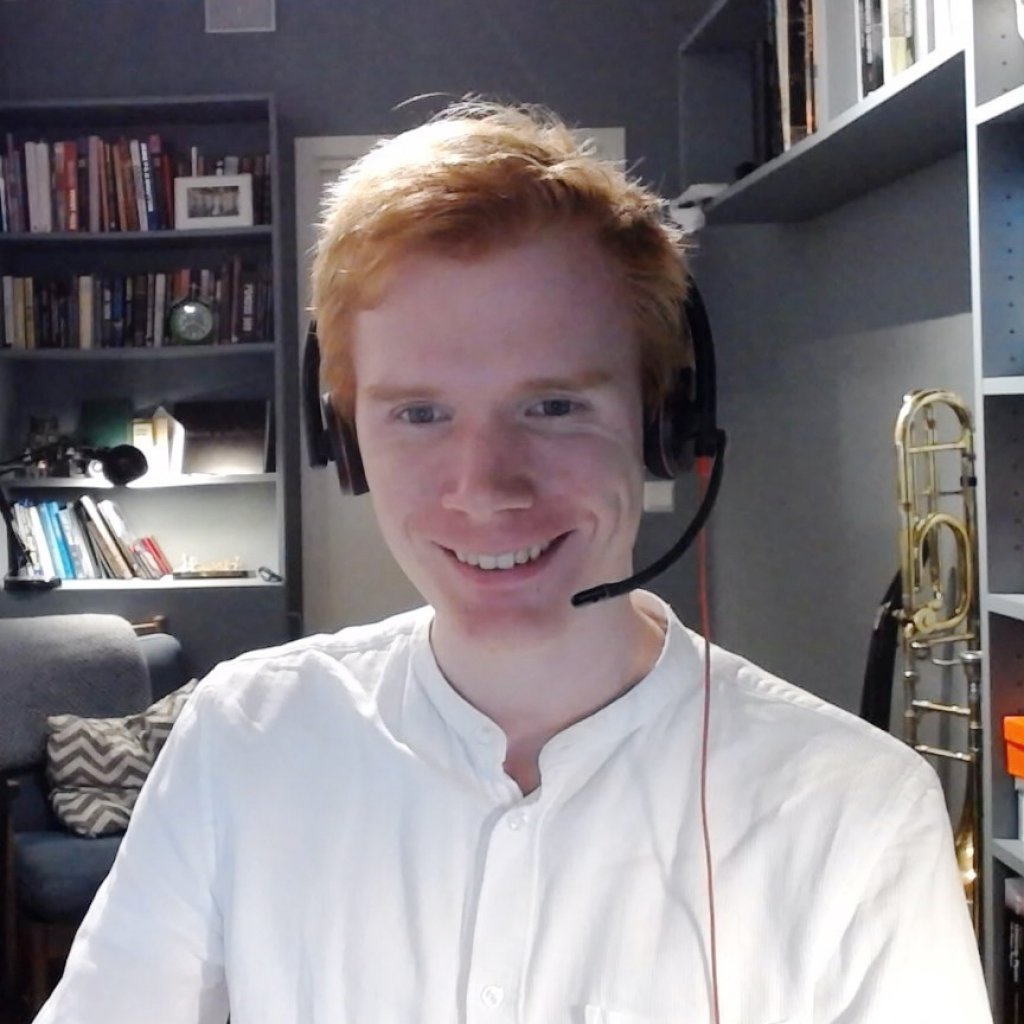
Øystein Barth Utbjoe
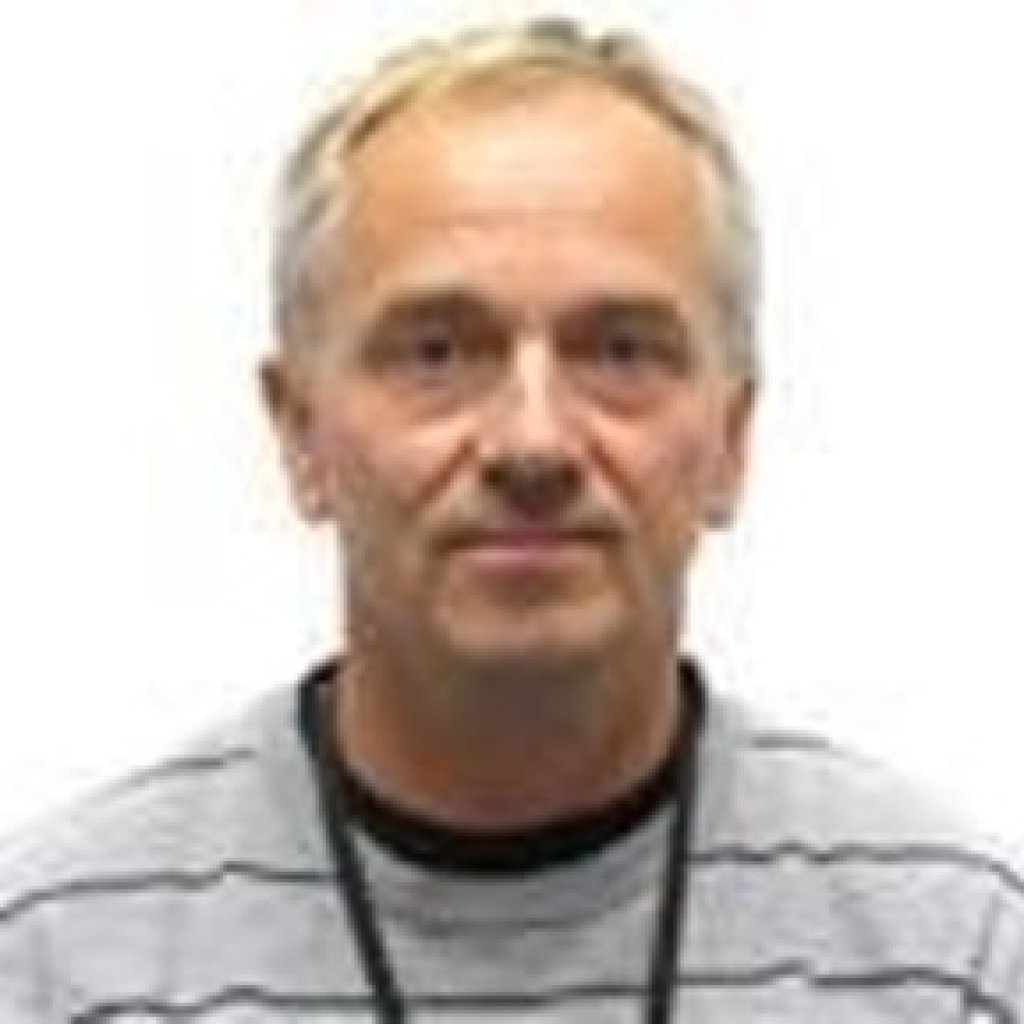
Erling Lunde
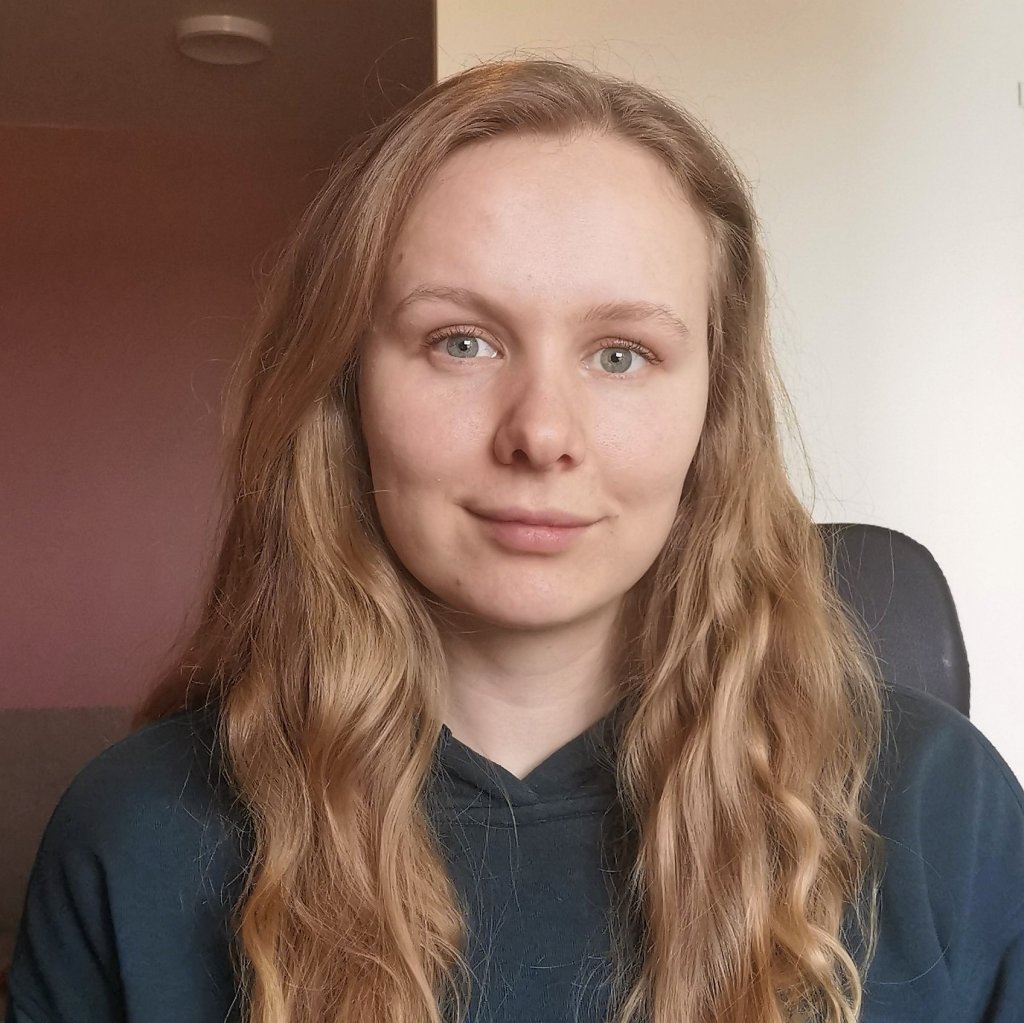
Edda Solem
Related stories
Showing stories for